Works completed (and on hold)

Marble tiling to common property walls and floor.

Revised plumbing.

Cracking to internal garage walls was partially repaired by strata in 2009 and 2011, and underpinned in 2015.

Marble tiling to common property walls and floor.
Lot 3 renovations, 2002
Lot 3 is the only unit to have been extensively renovated since the strata scheme was registered in 1994. It included the removal of load bearing walls, new tiling and waterproofing to walls and floors, new kitchen cabinets and laminate floors, revised plumbing and laundry location, wall rendering, acoustic underlay and more.
However, the acoustic underlay was removed by a new owner in 2010, and at the same time the kitchen bench, floor and other items were upgraded. Some of the 2002 works were also amended including the removal of gates blocking the path of egress and the submission of an engineer's certificate to Council.
The work was undertaken by m2design. Lot 3 also commissioned the Chapman Hutchison Report.
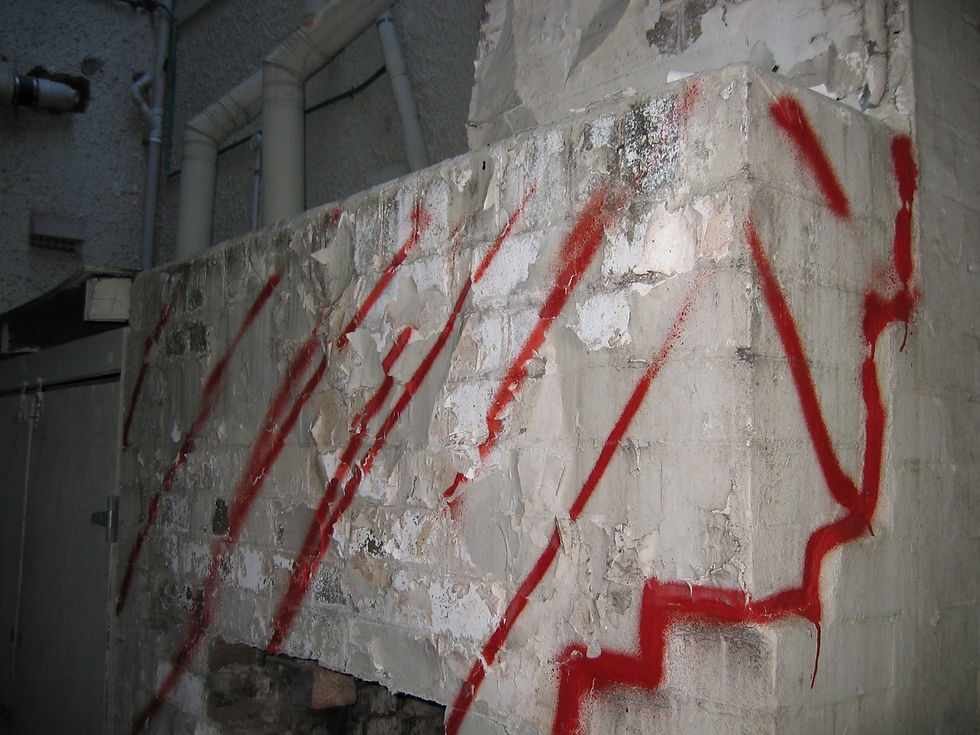
The engineers specified a new steel beam and brick structure.

Chimney base removed and temporary props installed.
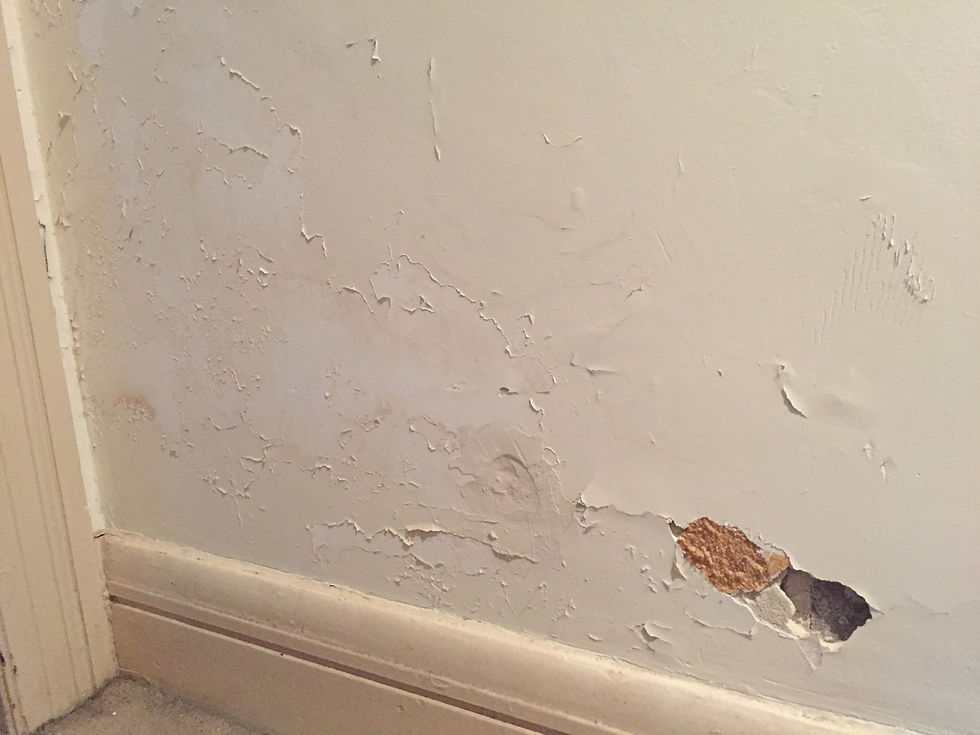
Internal walls have still to be repaired.
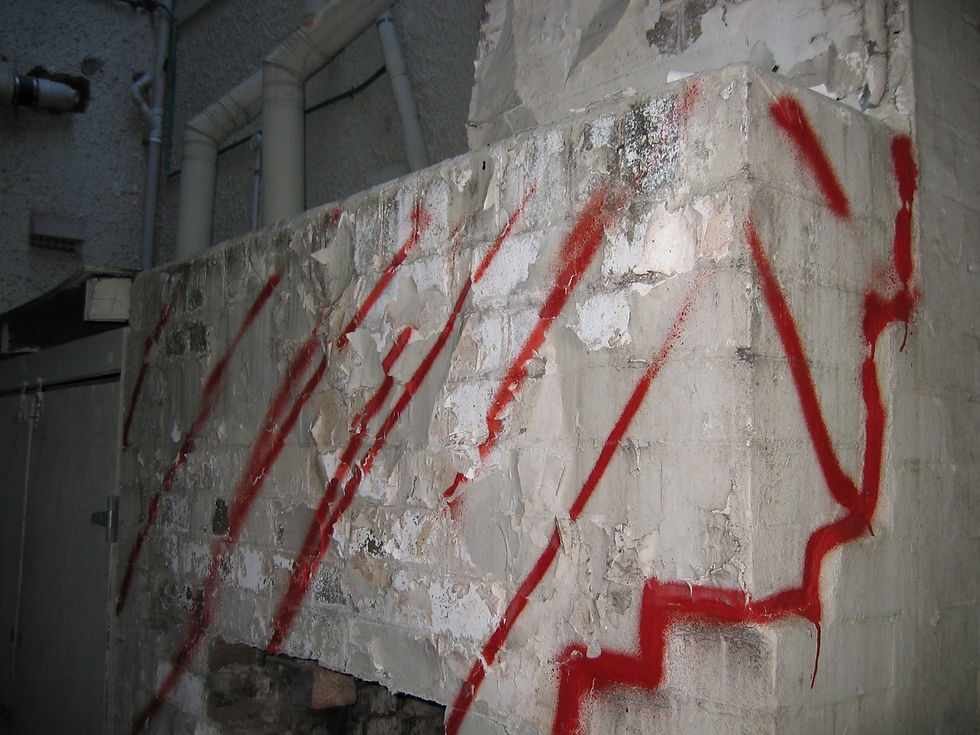
The engineers specified a new steel beam and brick structure.
Incinerator & chimney stack repairs, 2004
Northrop's engineers specified the detailed works to repair the structural damage to the incinerator chimney in the rear lightwell area. This work had been identified by Chapman Hutchison. The chimney base was opened up to reveal a mass of lime and ash slurry that acted as a sponge for rainwater and caused rising damp and soft brickwork in the adjacent walls. The new enclosure was designed with a louvre door to act as a new boiler house, and this was used until 2013.
The work was designed by Northrop and undertaken by BSR Construction. The rising damp and soft brickwork to the adjacent internal walls in Lot 1 is still to be repaired.

Western and southern strata boundaries.

Common property garden area.
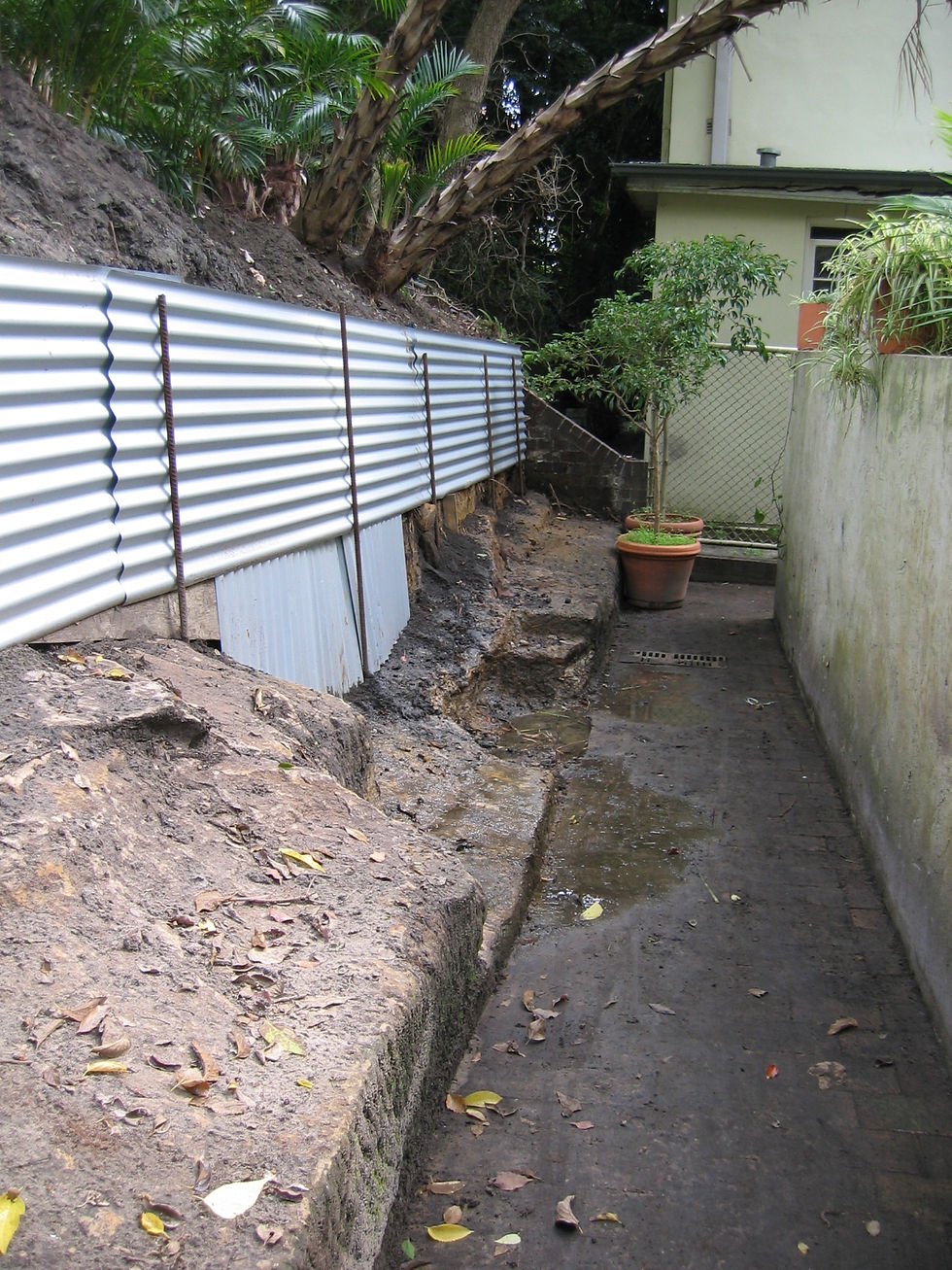
Temporary retaining wall extended into the common property area.

Western and southern strata boundaries.
Western boundary repairs, 2004
The steeply sloped land was cleared along the western boundary and damaged trees and failed retaining walls were removed prior to new terracing and planting.
About 40 new golden cane palms were planted and a new fence was installed along the entire strata boundary at a later date. The large camphor laurel tree in the common property garden was not removed until 2017.
This work was undertaken by BSR Construction with funding from Lot 1 and strata. The terracing to the common property garden is still to be completed.
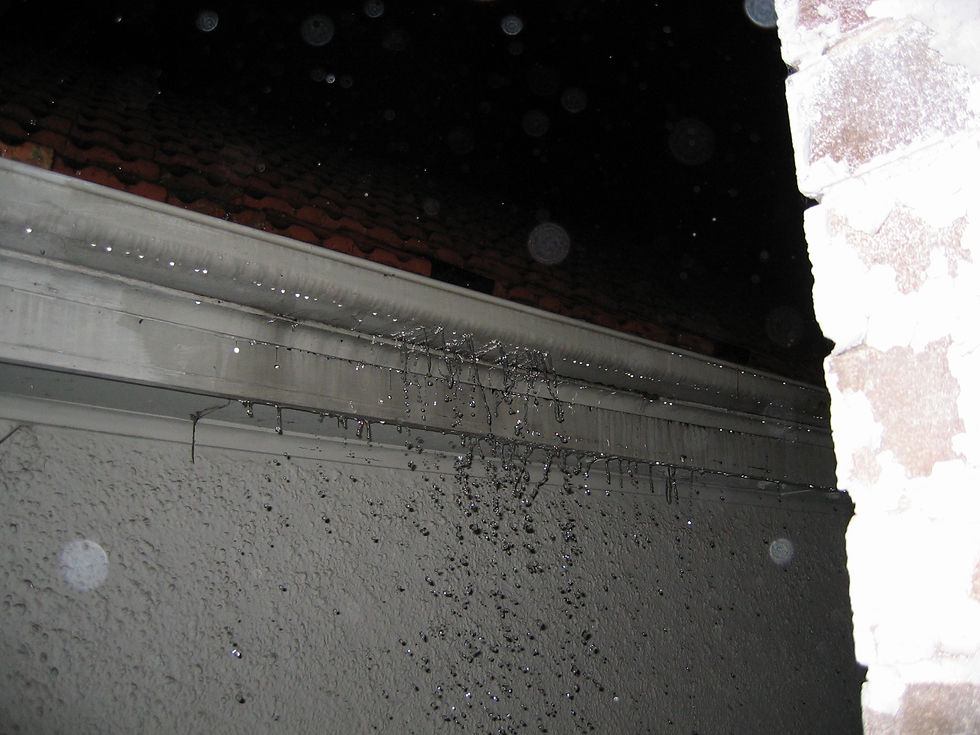
Caused by shallow gutters and a lack of downpipes.
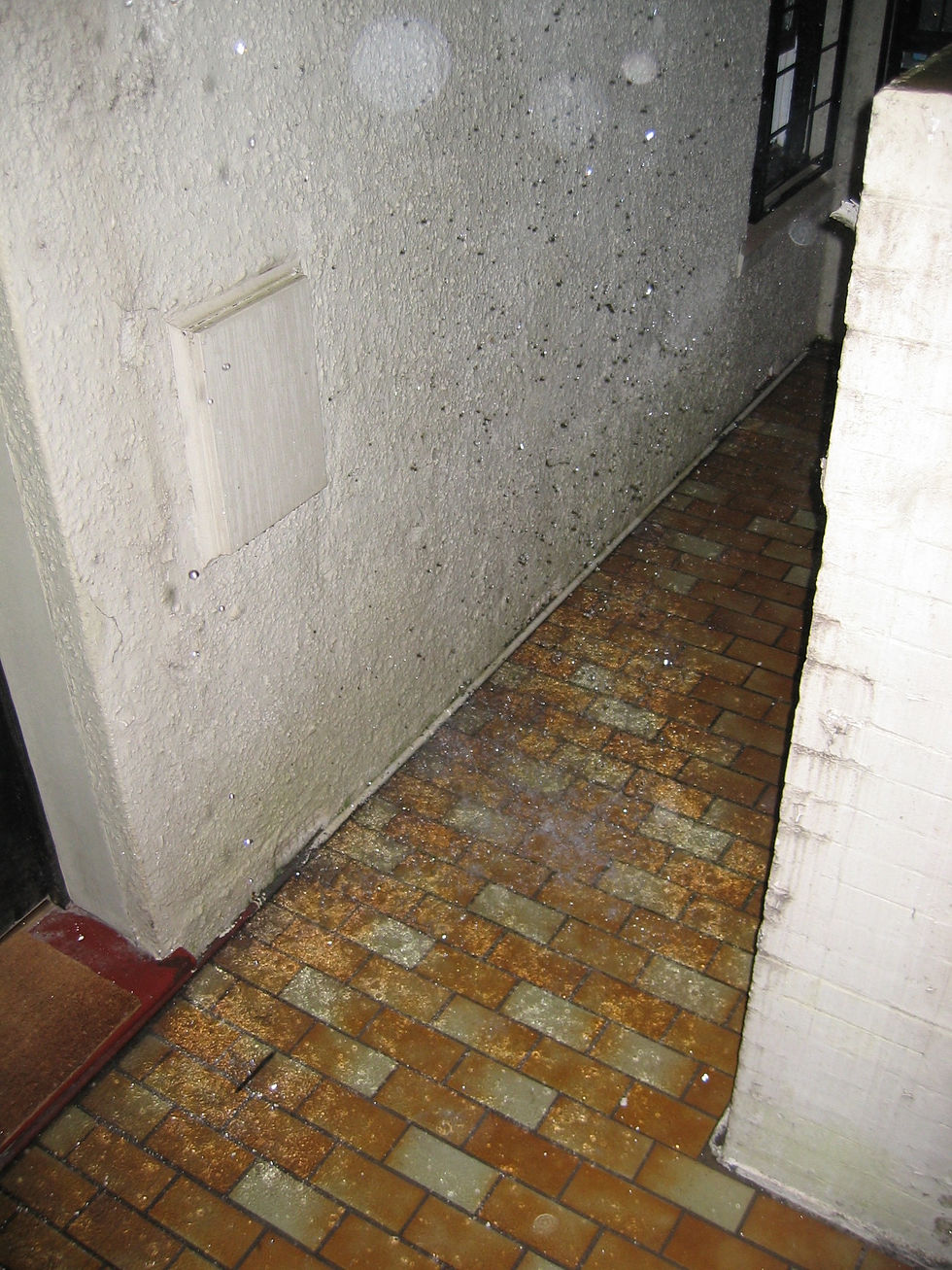
Contributes to rising damp in the light well area as the tile level is above the damp course membrane.
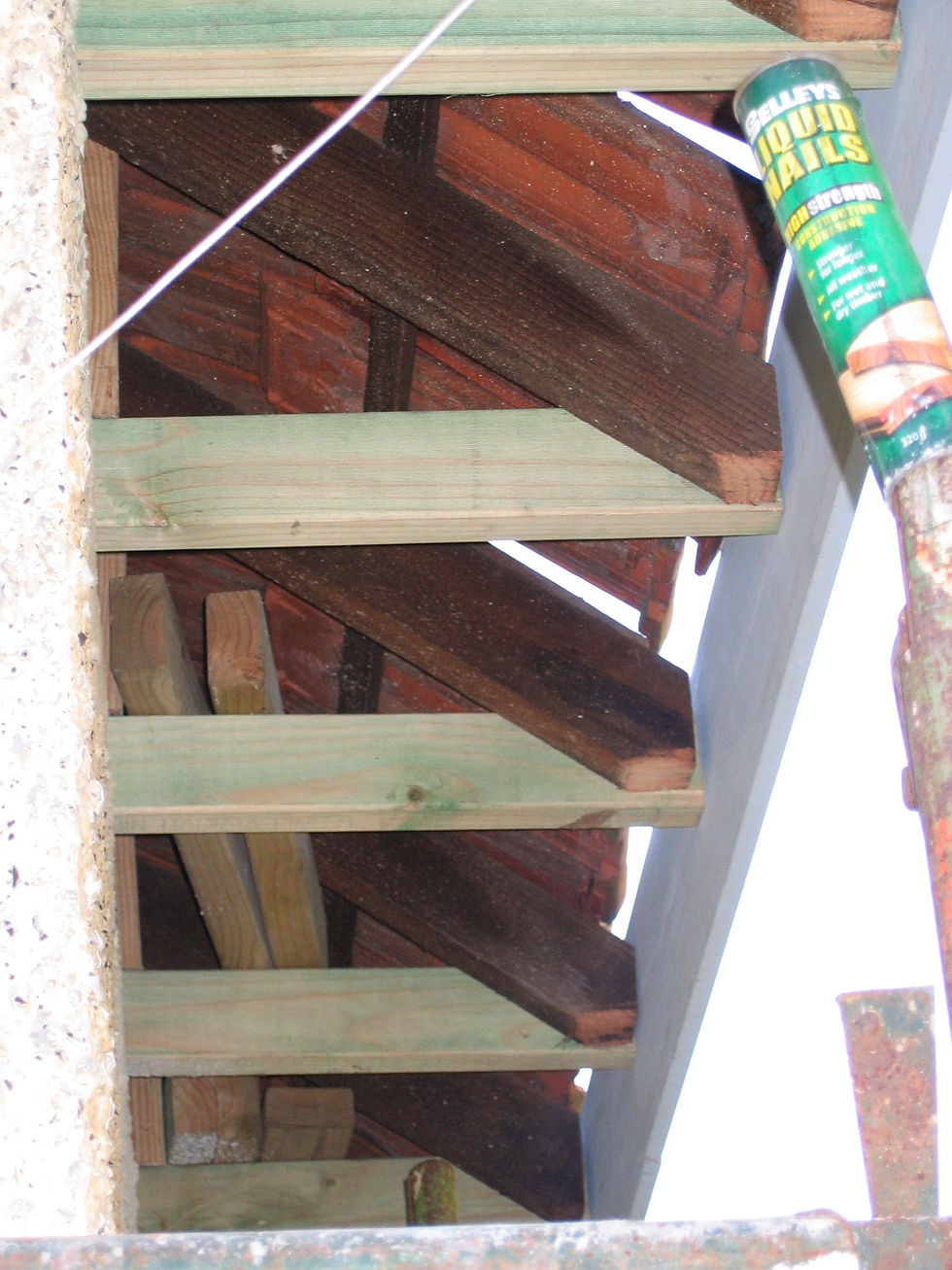
The eaves were rebuilt, and new gutters and downpipes installed.
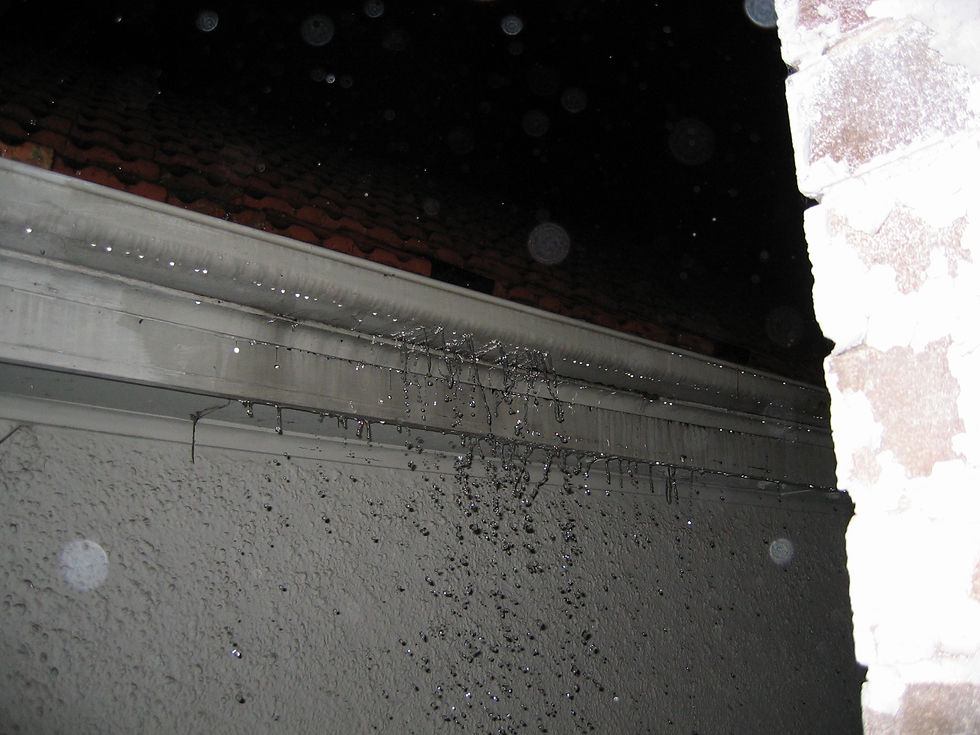
Caused by shallow gutters and a lack of downpipes.
Lightwell facade repairs, 2005
The original gutters from 1994, or eariler, were too shallow for the amount of rain being collected from such a large roof. This meant that overflowing water was rotting the fascia boards. Where the rot was most prevalent was in the lightwell area where the roof valleys directed a higher proportion of the rainfall.
To address the recommendations in the Chapman Hutchison Report, the lightwell area was filled with scaffold and the gutters were removed. New fascia boards, soffits and deeper gutters were installed. An additional downpipe was also installed to help get the water away. The painted membrane was also renewed but the old calcimine base paint was not removed as part of the process.
The work was undertaken by BSR Construction.

Original clay pipes exposed.

Gas and water pipes were replaced with copper.
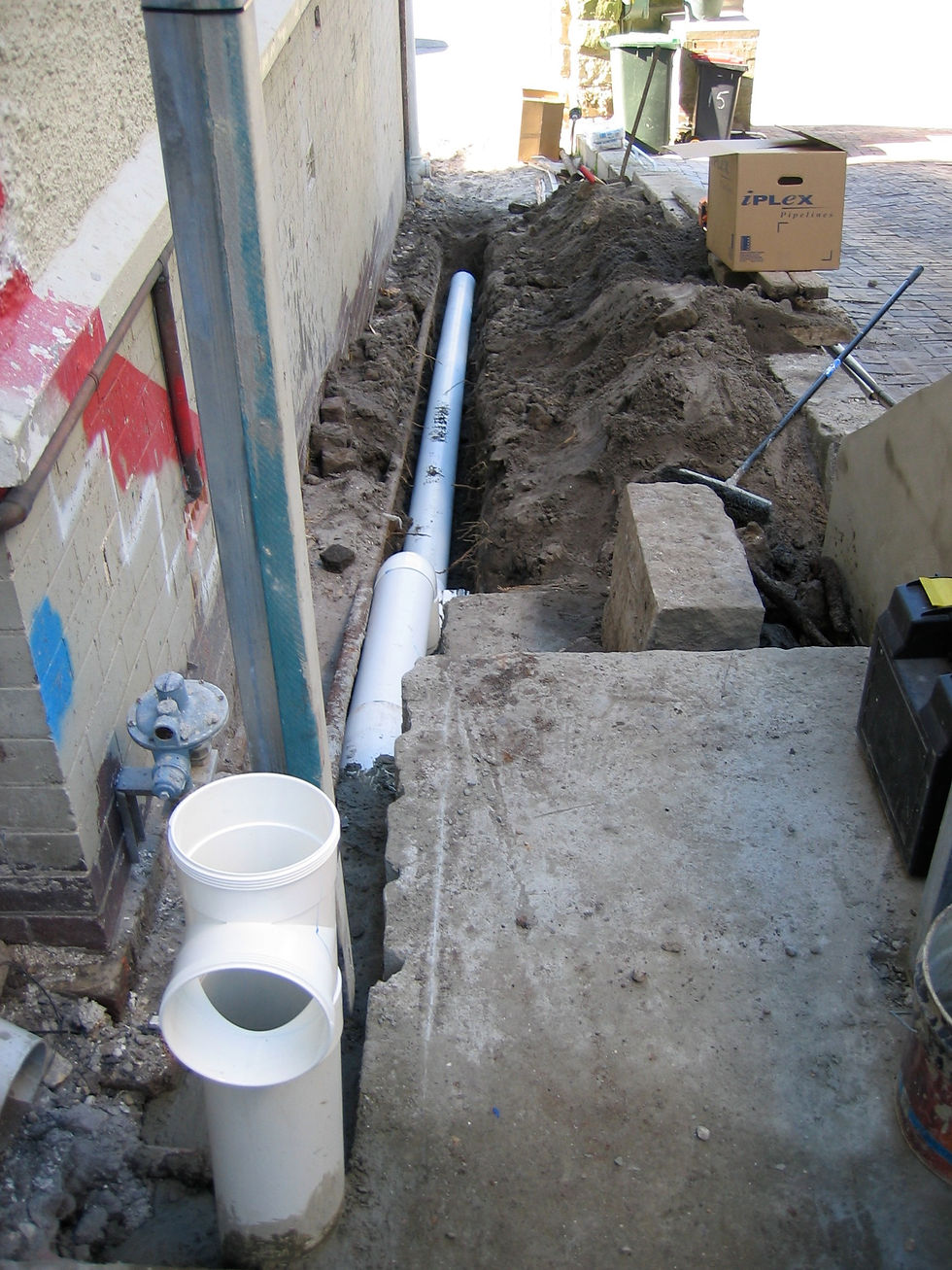
New 150mm drainage under common property area.

Original clay pipes exposed.
Southern storm water upgrade, 2006
A civil/hydraulic engineer was engaged to upgrade the storm water system ahead of a bedroom extension and new roof to Lot 1. This was part of Condition 13 in DA322/2004/1. The storm water and groundwater was directed through a new 150mm pipe and out to the kerb line on Manning Road.
At the same time a new sewer line was connected to an existing branch running under the foundations, and then extended to the boundary trap in 2015 via the driveway sewer system.
All work was undertaken by George Holovsky with funding from Lot 1 (cost $5,400). Special By-Law 1 covers these works.

Southern retaining wall in 15 Manning Road (the boundary line is the face of this wall).

Large kerb stones on elevated dirt bank (face of the kerb stone is the boundary).

Completed retaining wall with brush fence in 2007 (painted blockwork face is the boundary line).

Southern retaining wall in 15 Manning Road (the boundary line is the face of this wall).
Southern boundary repairs, 2006
The property boundaries are the responsibility of the owners corporation and the southern boundary walls relied on sandstone blocks that were either displaced or temporarily propped. Whilst retaining a sandstone theme, Alba & Associates designed a new boundary wall that provided a wider driveway to 15 Manning Road and gave more space for the planned additions to Lot 1 in 2007.
The work was paid for by Lot 1 in exchange for the exclusive-use of 2.6 metres of common property adjacent the southern gas meters (cost $19,000). The structural work was designed by Alba & Associates and constructed by George Holovsky. Special By-Law 1 covers these works in addition to a written consent from 15 Manning Road.

Planned removal of the raised garden area to allow for timber decking.

Planned removal of an existing laundry house.
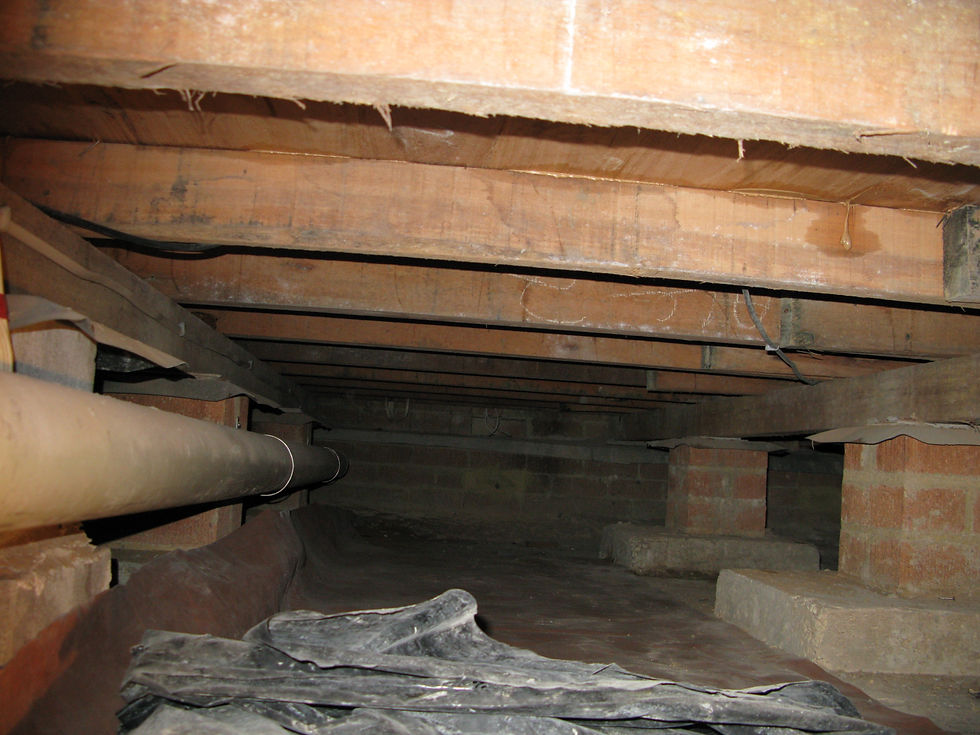
Termite caps and an accessible subfloor area.

Planned removal of the raised garden area to allow for timber decking.
Lot 1 bedroom extension & second bathroom, 2007
The original courtyard to Lot 1 consisted of a small laundry out-house on the back of bedroom 3 and a large paved area.
The laundry was demolished and replaced with a larger room and walk-in wardrobe. Special By-Law 1 covers these works as well as the southern sewerage and storm water upgrade (2006) and the southern boundary repairs (2006). The gas meters were relocated and all regulators upgraded.
The work was designed by Dunn Architects and Alba & Associates, constructed by George Holovsky, and reviewed by Albert Zenere. All works were funded by Lot 1 (cost $111,695).
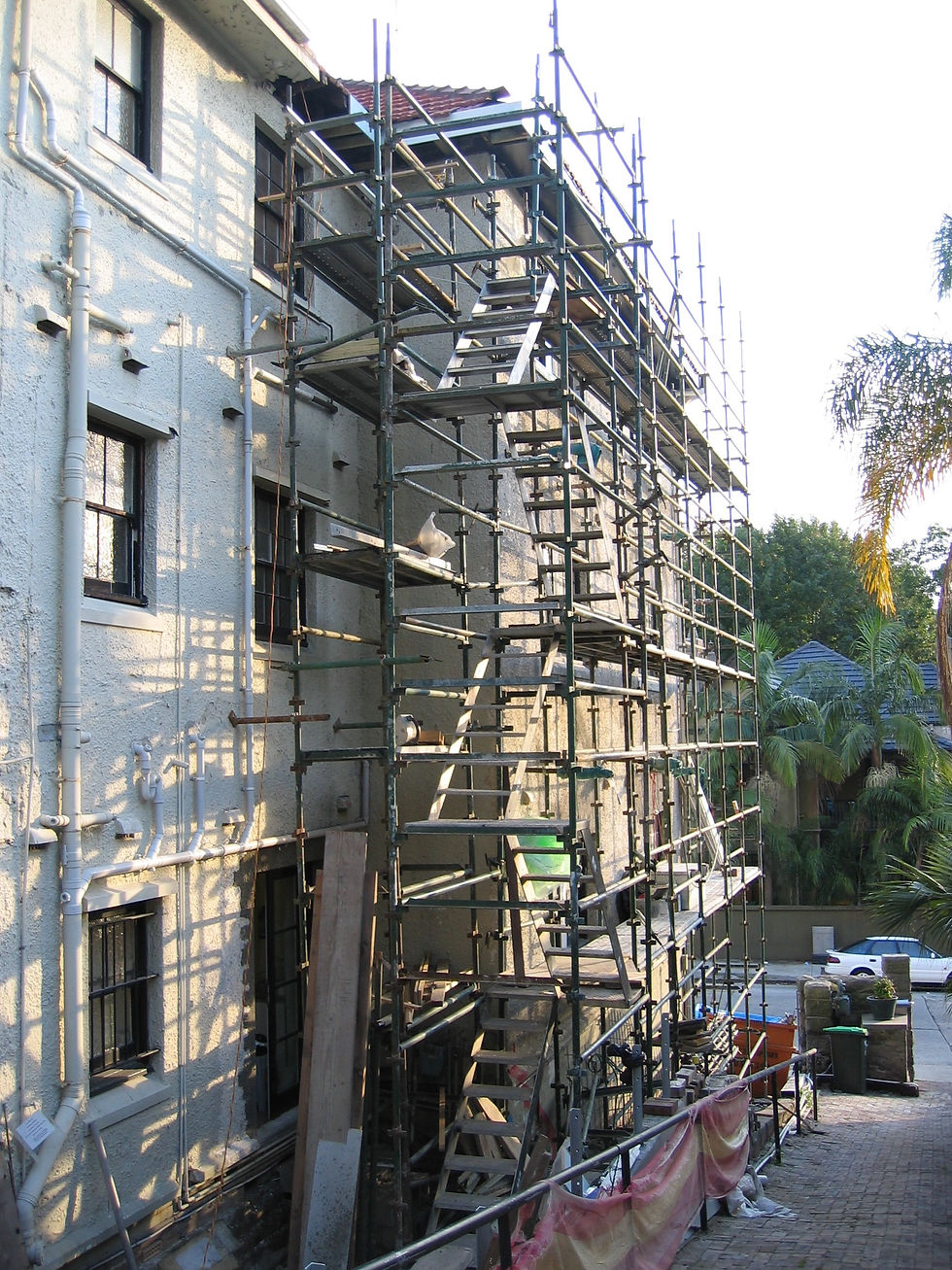
The scaffolding was done in stages and moved as the work progressed.
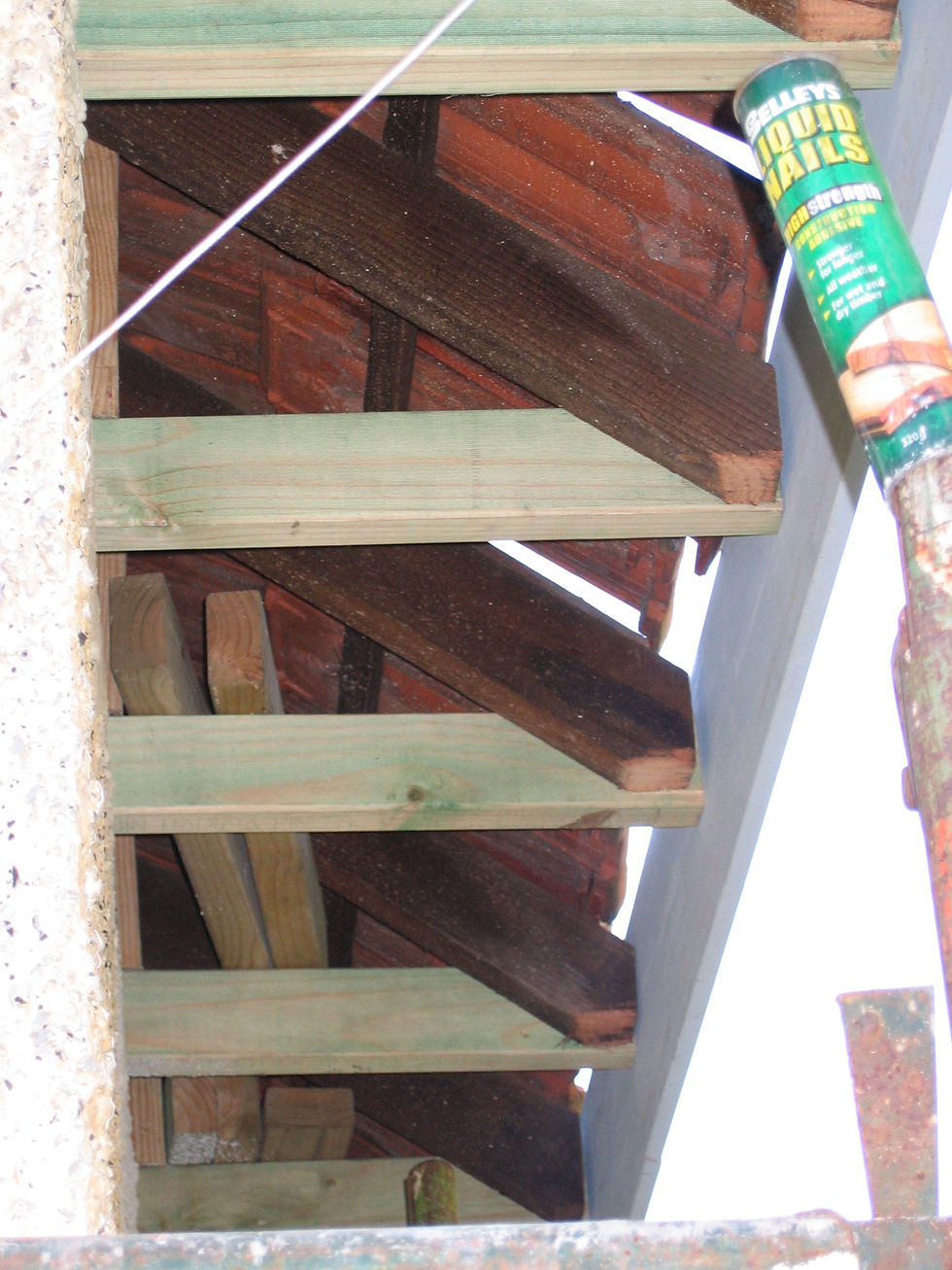
The timber eaves were rebuilt, and gutters and downpipes replaced.

Pressure blasting the old paint layers to get back to the bare render.
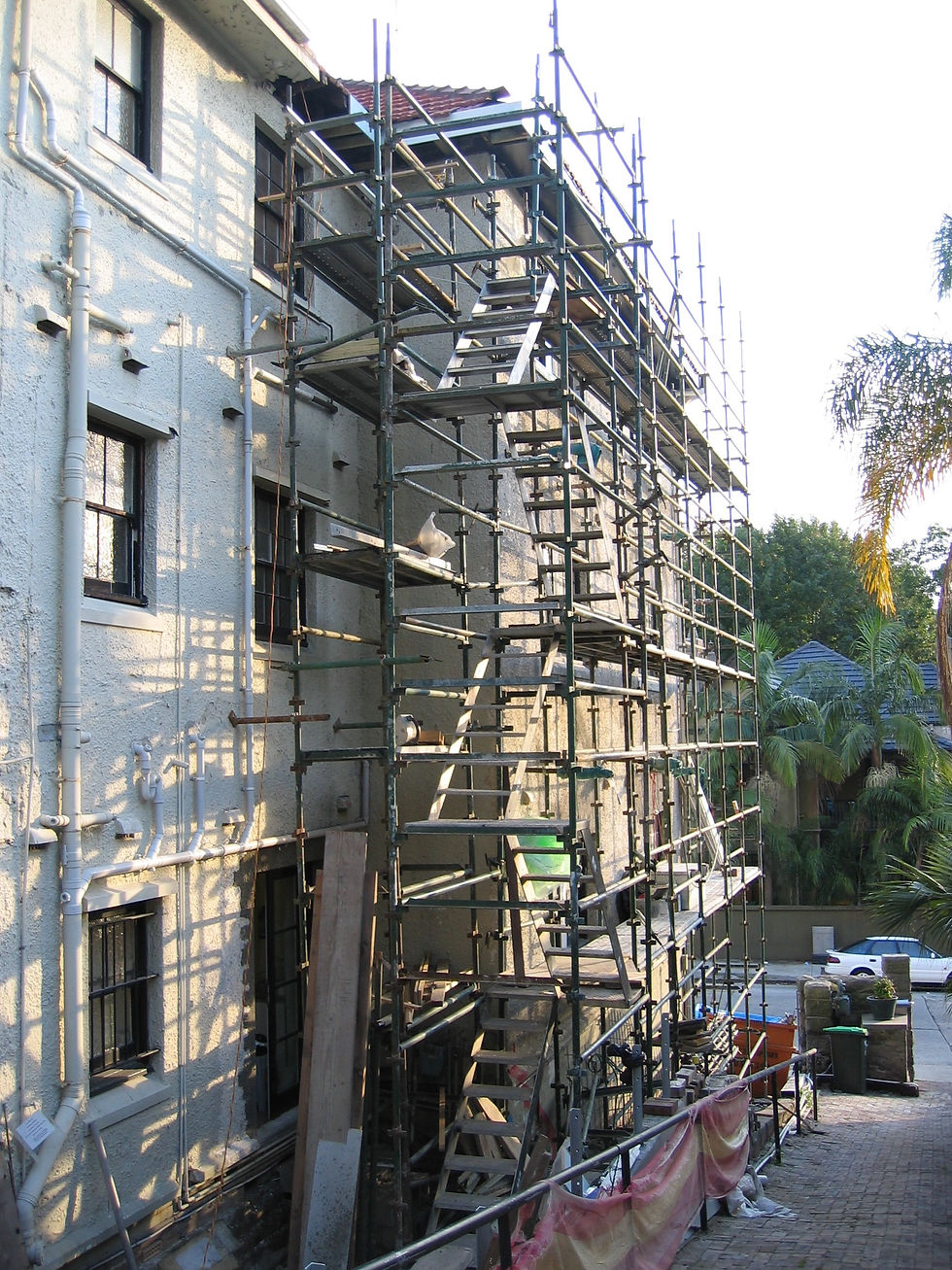
The scaffolding was done in stages and moved as the work progressed.
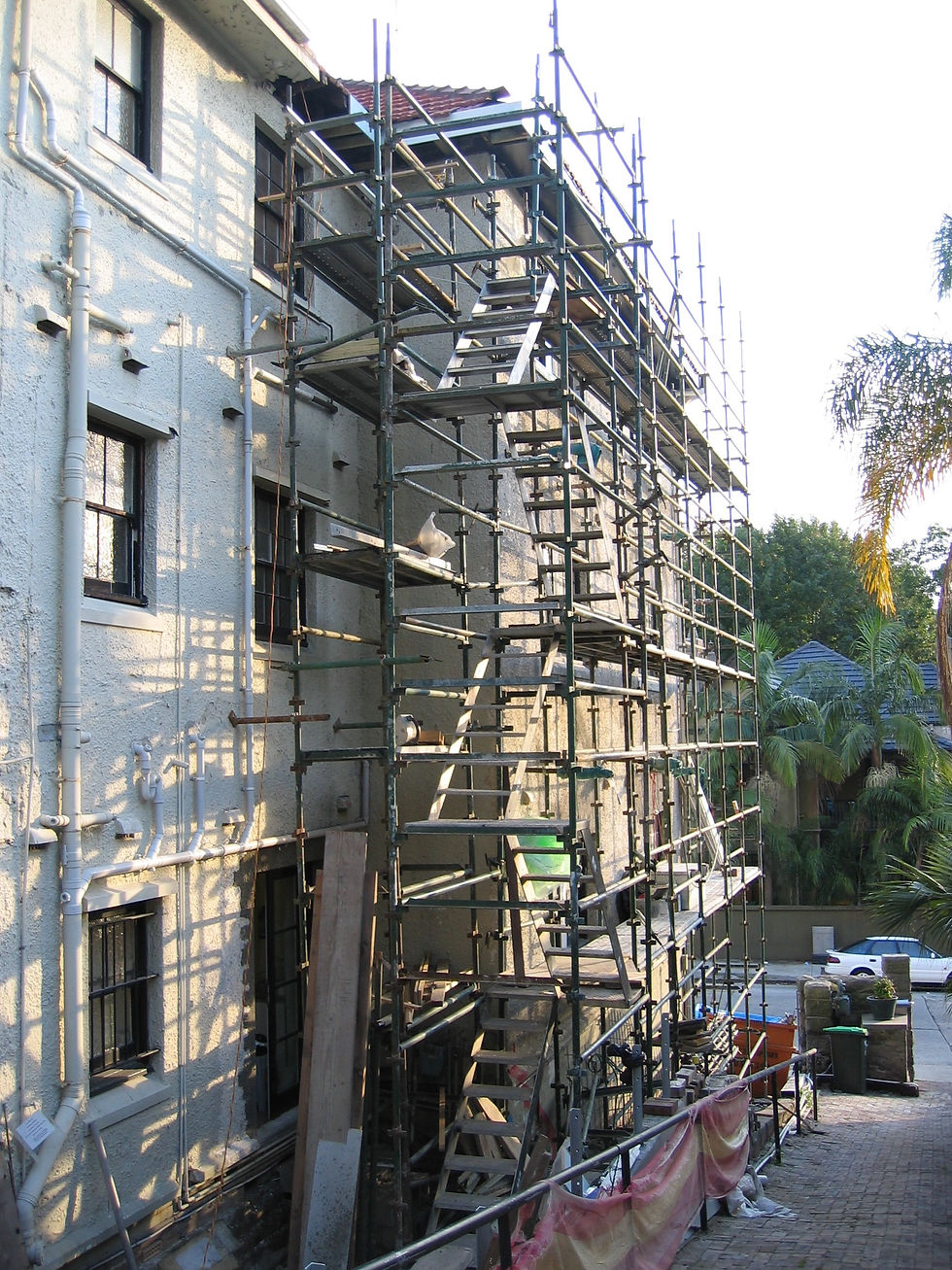
The scaffolding was done in stages and moved as the work progressed.
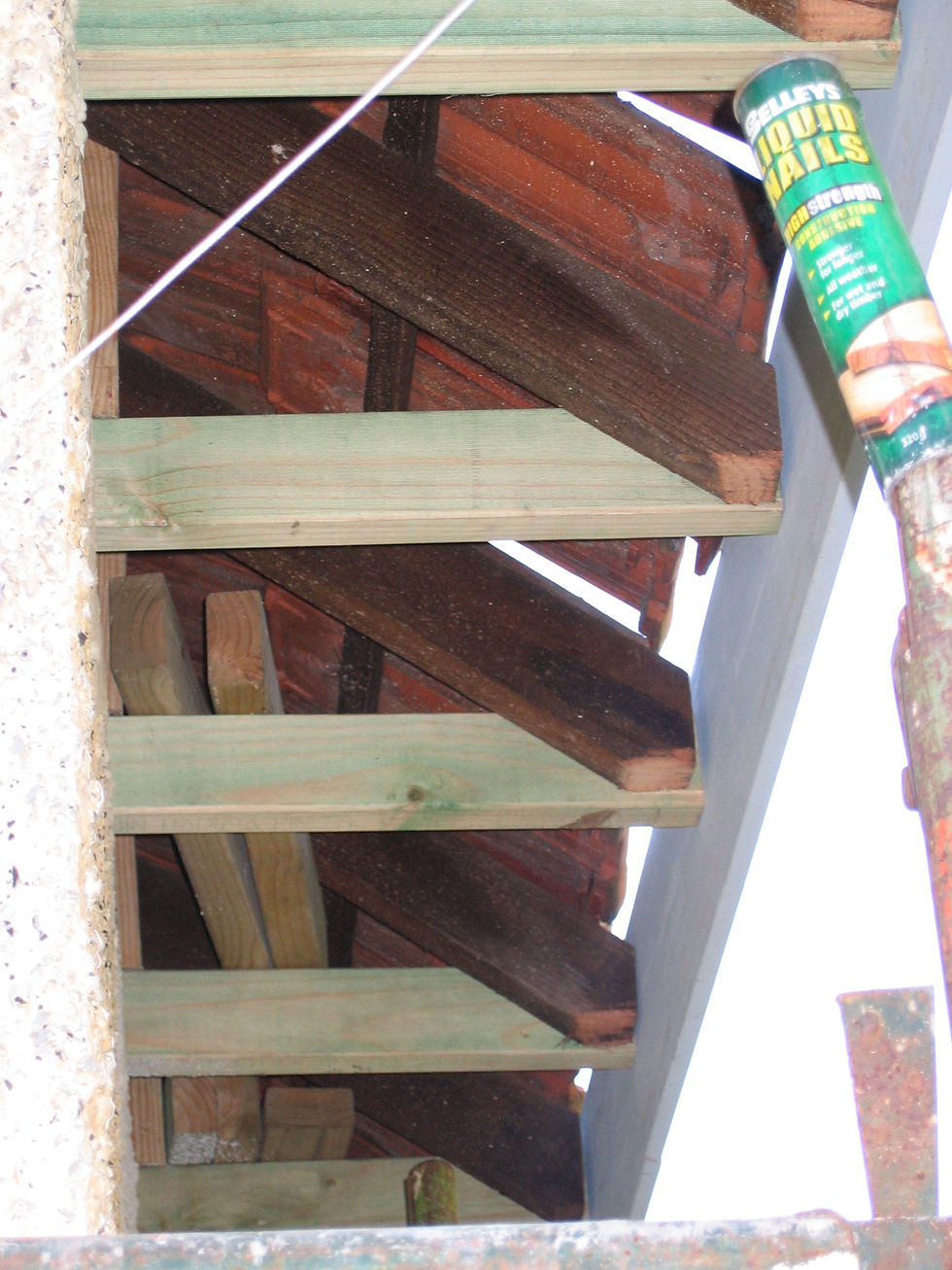
The timber eaves were rebuilt, and gutters and downpipes replaced.

Pressure blasting the old paint layers to get back to the bare render.
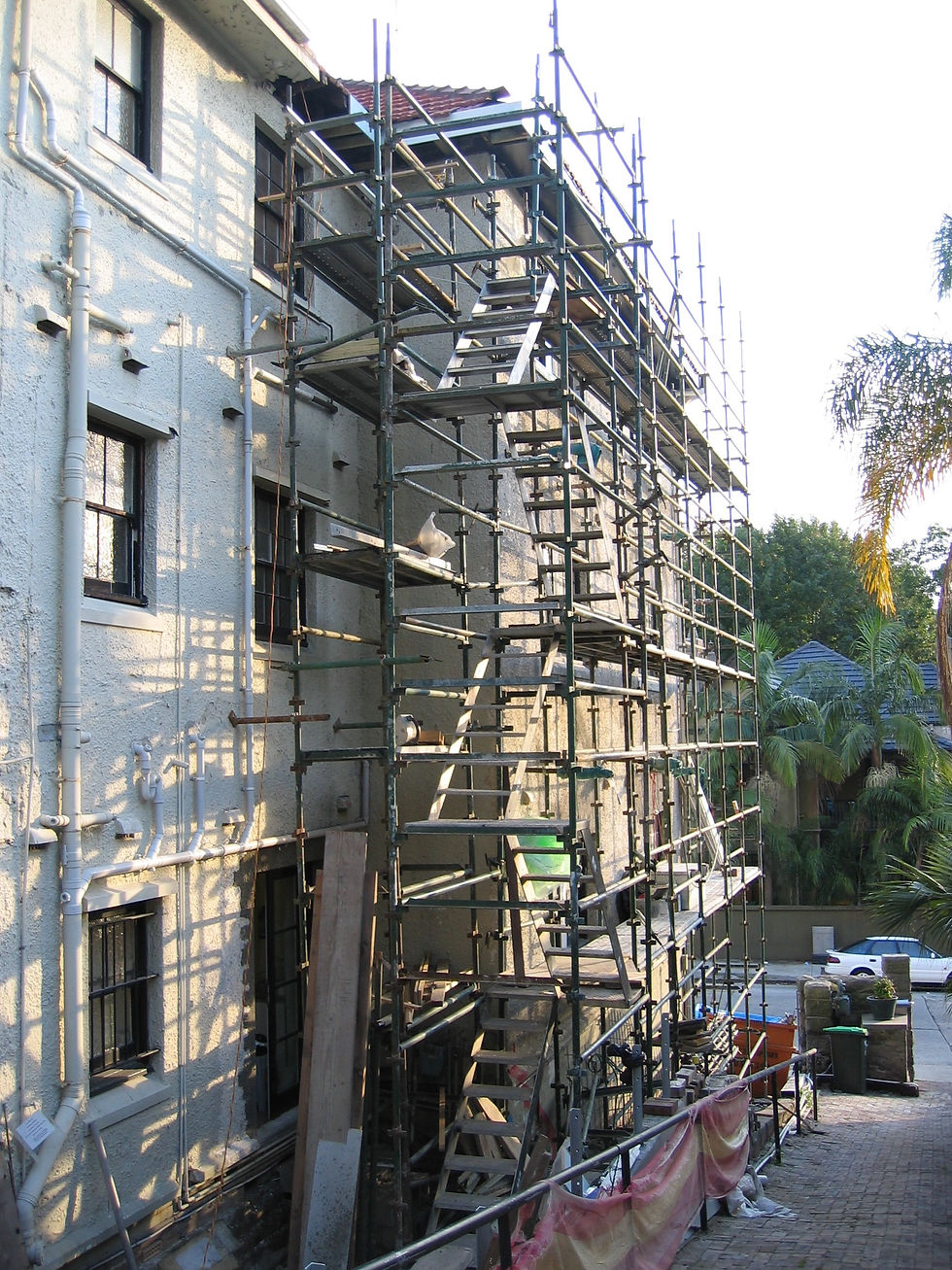
The scaffolding was done in stages and moved as the work progressed.
Southern and western facade repairs, 2007
In 2007 the entire southern and western facades were covered in scaffold to address the recommendations in the Chapman Hutchison Report. The eaves and gutters were replaced; all external structural cracking was filled with Sika grout; any failed lintels above windows were replaced; all plumbing was replaced; and, the entire facade was pressure blasted back to the calcamite covered roughcast render. The walls, windows and other timber were re-painted.
The work was undertaken by BSR Construction and reviewed by Albert Zenere. The structural repairs to the inner leaf of the external wall have still to be undertaken in all Lots.
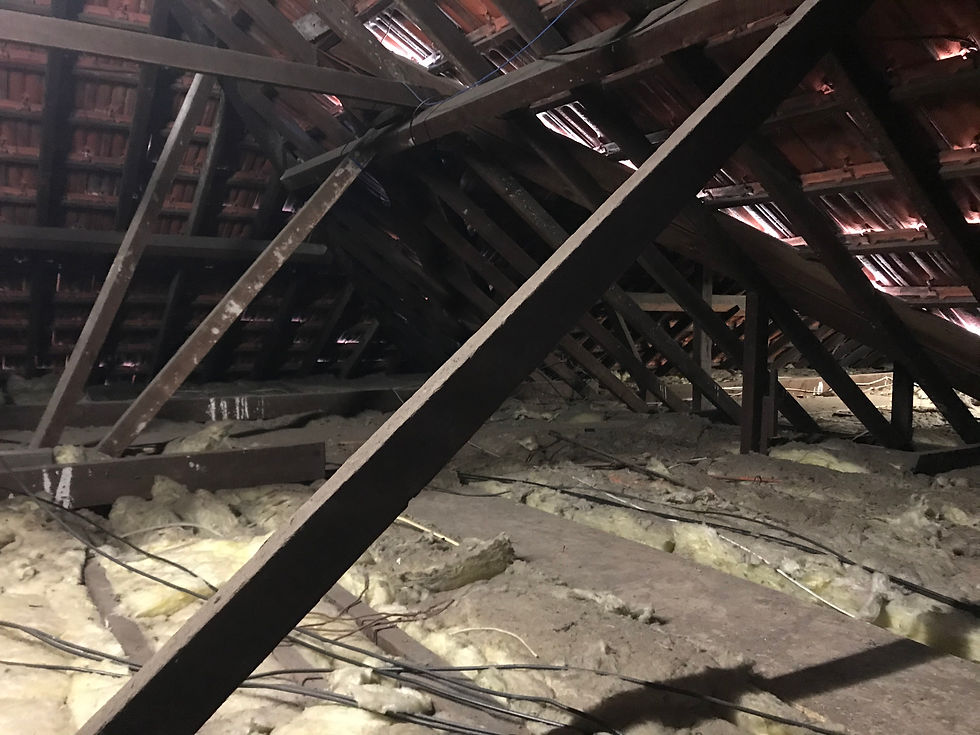
The roof timbers are slowly moving due to the iron nails rusting over 90 years.

Lime mortar reacts with pollutants and breaks down leaving sizeable gaps. An acrylic render was used to seal the brickwork and lime mortar.

Roof access is via a drop down ladder and ceiling trap door.
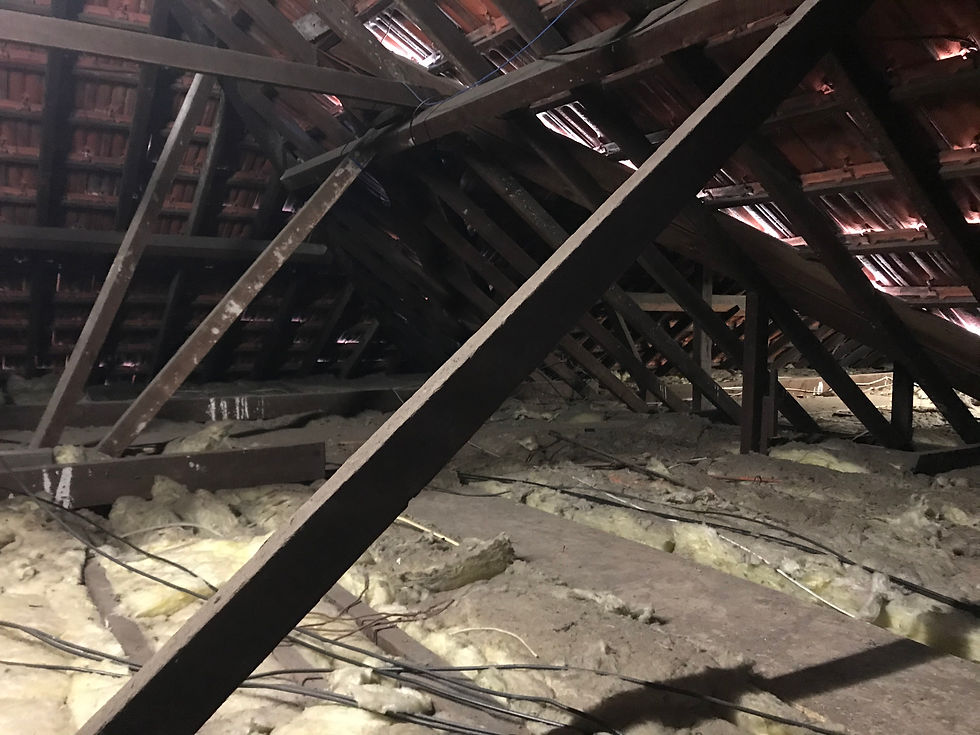
The roof timbers are slowly moving due to the iron nails rusting over 90 years.
Roof access, insulation and gable wall repairs, 2009
In 2009 access to the roof void was created via a new door and a NSW home insulation grant was used to insulate the roof void. The roof space was full of old tanks and cabling, and 80 years of black soot. Some of this was removed and 100mm of insulation installed together with some walkways and lighting. The lime mortar in the gable walls was badly eroded and so each gable was acrylic rendered on the inside.
The roof is still unlined (i.e. there is no sarking under the roof tiles) and so the black soot continues to accumulate and will do so until the roof tiles are replaced. The roof is the original dating back from 1928 and in 2018 a structural engineer reported that the roof timbers were moving because the original roofing nails were rusting through.
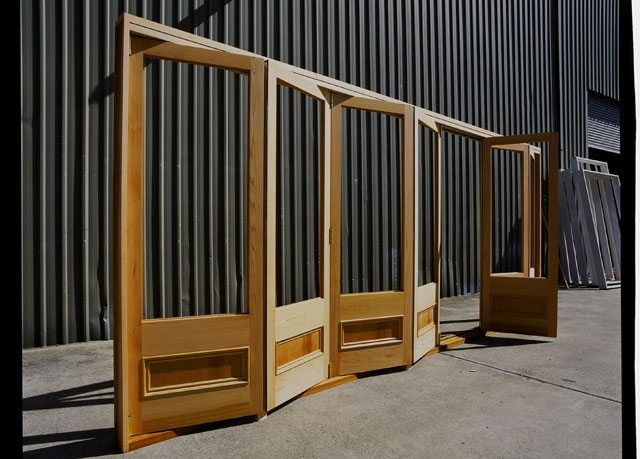
All these works were put on hold in 2009.
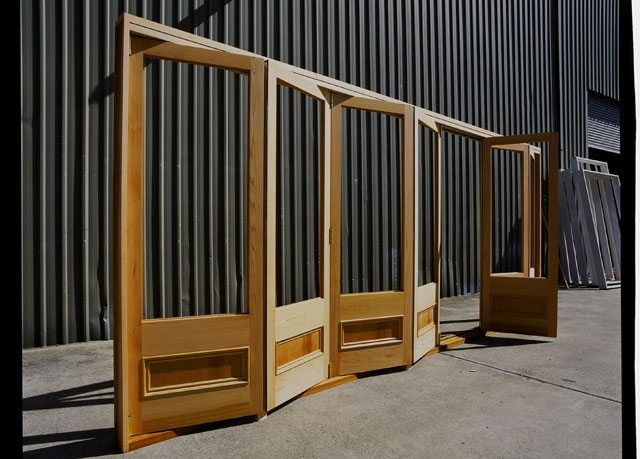
All these works were put on hold in 2009.
Lot 1 renovations (on hold from 2009)
These works are described in Special By-Law 2 and started in 2008. The en-suite bathroom in the bedroom extension was abandoned and a Section 96 was approved by Woollahra Council for a new bathroom (to replace bedroom 2). However, in 2009 Lot 1 put these works on hold until the following had been completed:
1. Hot water system upgrade (completed 2013)
2. Extending the southern sewer line upgrade to the boundary trap (completed 2015)
3. Structural underpinning of the brick columns either side of the kitchen wall openings (completed 2015).
In 2019 the new bathroom to Lot 1 was completed as part of DA 322/2004/3 and a building certificate was issued by Woollahra Council.
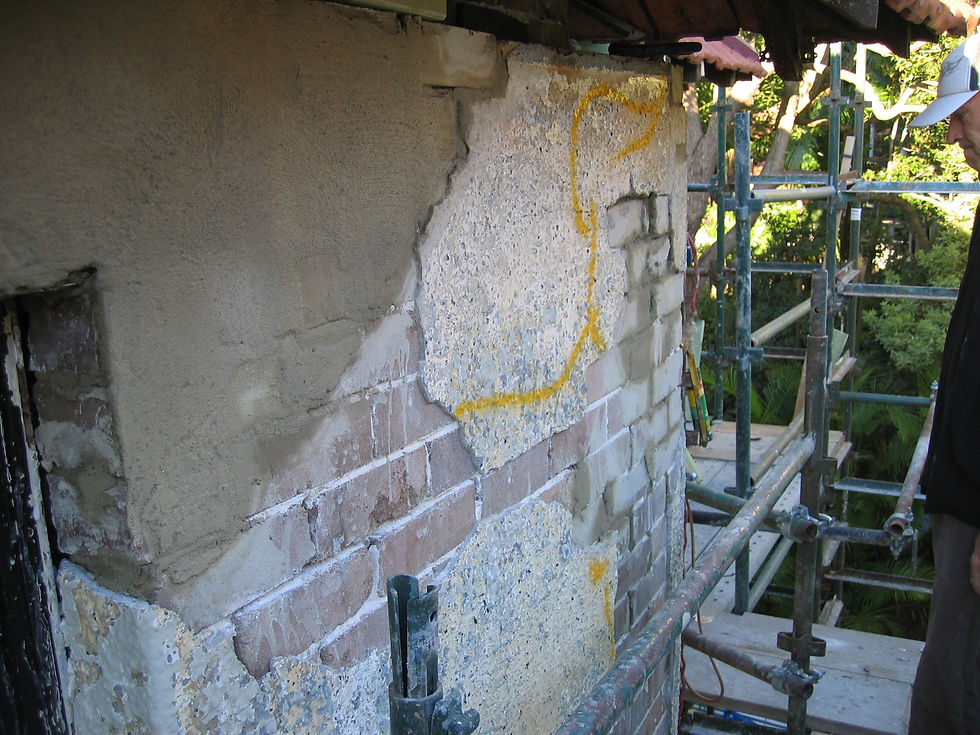
Removing the roughcast render to repair the cracking.

Across all facades, about 45 of the 70 lintels had failed.
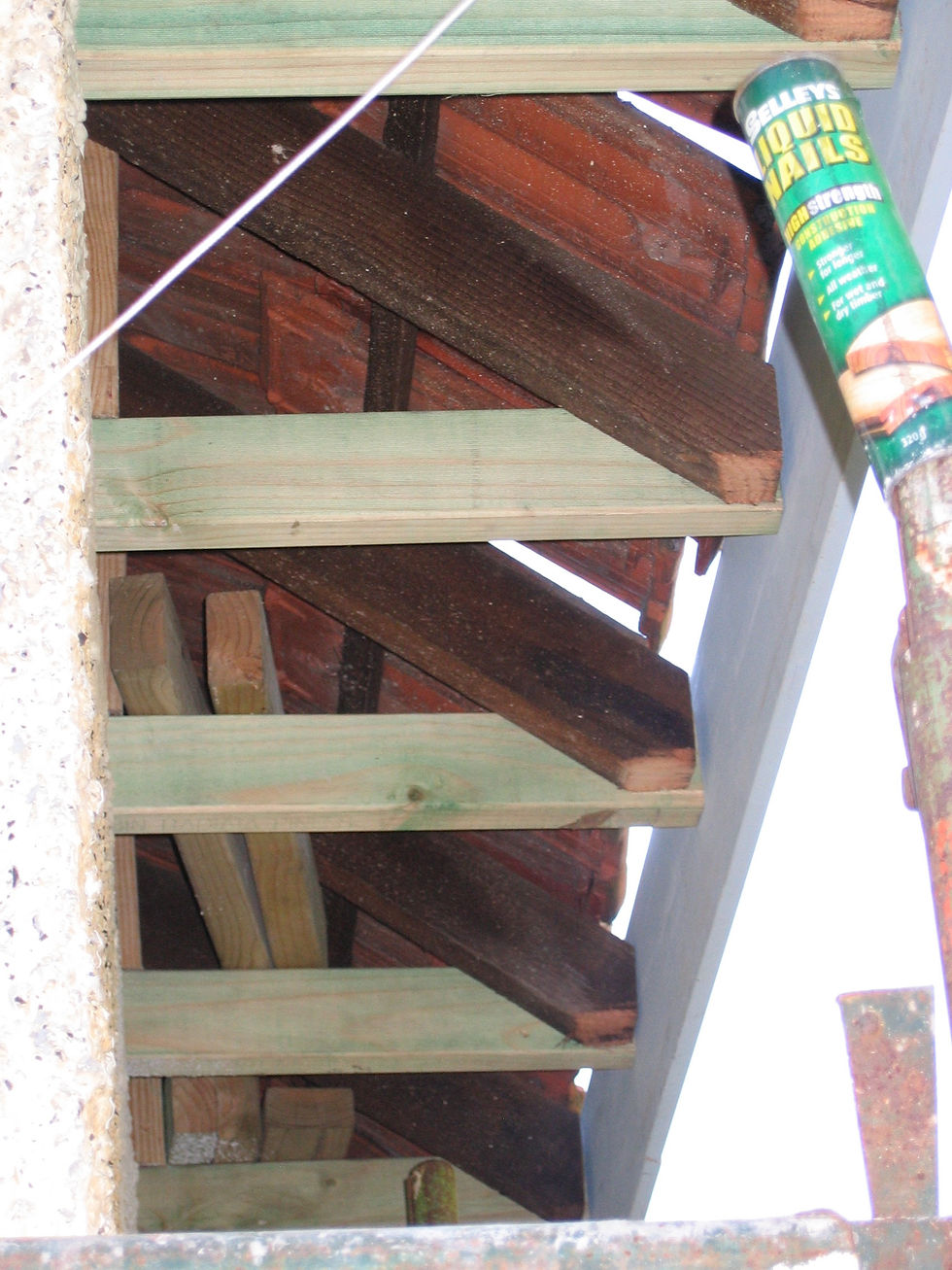
The eaves were rebuilt, and the gutters and downpipes replaced.
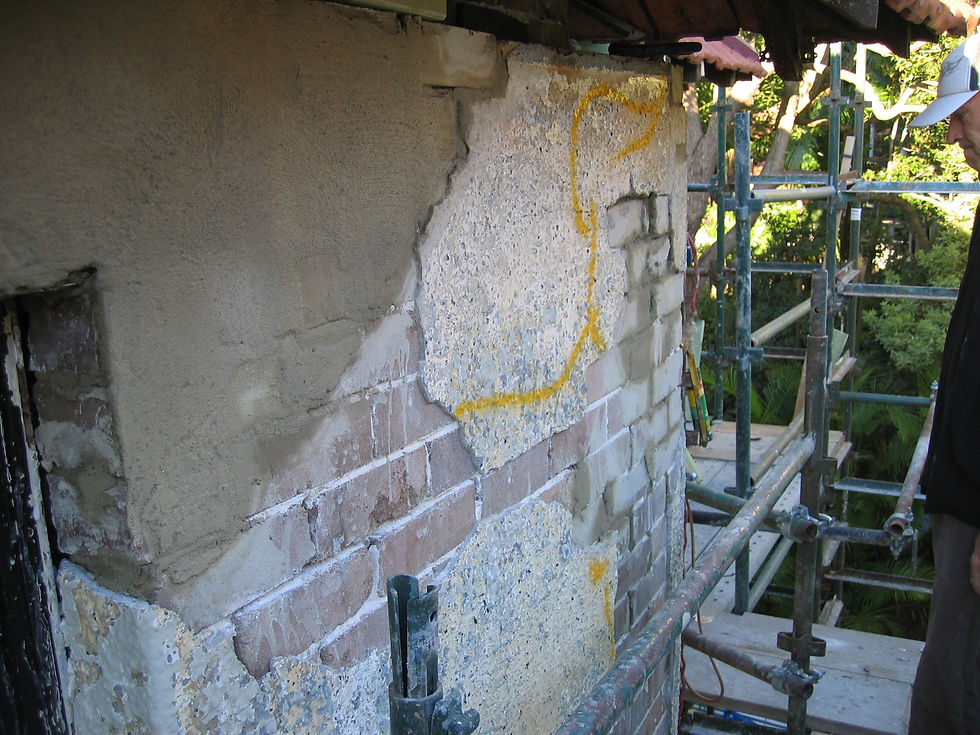
Removing the roughcast render to repair the cracking.
Northern facade repairs, 2009
As recommended in the Chapman Hutchison Report, and consistent with the works to other facades, in 2009 the northern facade was covered in scaffold and the external structural repairs undertaken.
Building movement on the northern side of the building is at greater risk than the southern side due to the underlying groundwater conditions. The building has dropped about 70mm on the northern side and this meant that the scope of structural repair was far greater.
The work was undertaken by BSR Construction. The structural repairs to the inner leaf of the external wall have still to be undertaken in all Lots.

Similar cracks exist on the internal leaf of the cavity wall, hidden behind 'drummy' plaster.
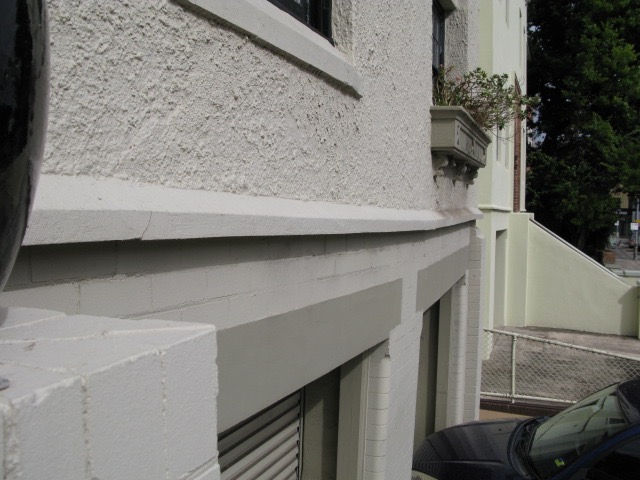
A major cause of the cracking was the 50mm to 70mm of footing movement.

The internal cavity leaf of the brick wall is only accessible from inside units.

Similar cracks exist on the internal leaf of the cavity wall, hidden behind 'drummy' plaster.
Eastern (front) facade repairs, 2010
Consistent with the Chapman Hutchison Report, in 2010 the external structural repairs were undertaken to the eastern (front) facade. The amount of building settlement on the right hand side was extreme, and much of the cracking required brickwork to be rebuilt. Failed clinker ash lintels to roof corbels and brick arches made this facade very challenging for repairs. The vibration from the voids under concrete slabs in Manning Road can be felt in the building and this may be a contributing factor to the cracking.
The work was undertaken by BSR Construction. The structural repairs to the inner leaf of the external wall have still to be undertaken in all Lots.

Impact of building settlement in garage of Lot 2.

Impact of building settlement in front bedroom of Lot 2.
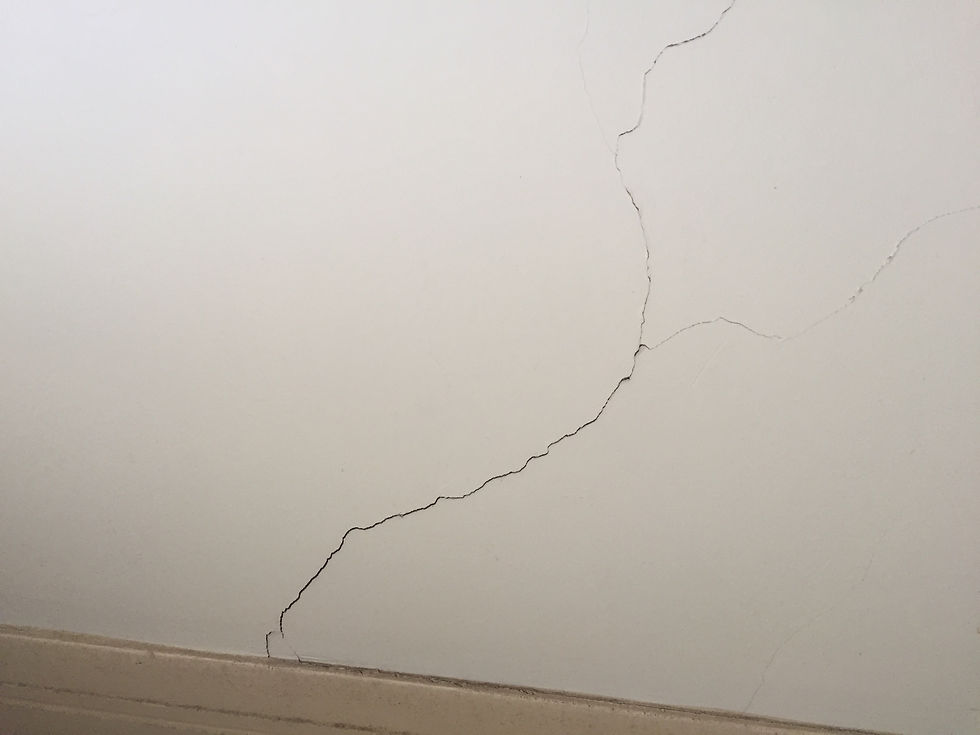
Structural cracking hidden behind plaster.

Impact of building settlement in garage of Lot 2.
Internal structural repairs (on hold from 2010)
The structural repairs needed to internal walls and the inner leaf of the cavity wall have been on hold since 2010. Most are disguised behind drummy plaster and the work on the external facades between 2007 and 2010 provides an indication of their scale and magnitude. The inner leaf of the cavity wall is less vulnerable to water ingress, but carries more weight than the outside wall because of the load from floor and ceiling joists.
Whilst the internal leaf of the cavity wall is the property of the owner's corporation, the internal walls are the property of Lot owners. The Chapman Hutchison Report provided two repair methods for Lot owners to follow when repairing internal walls.
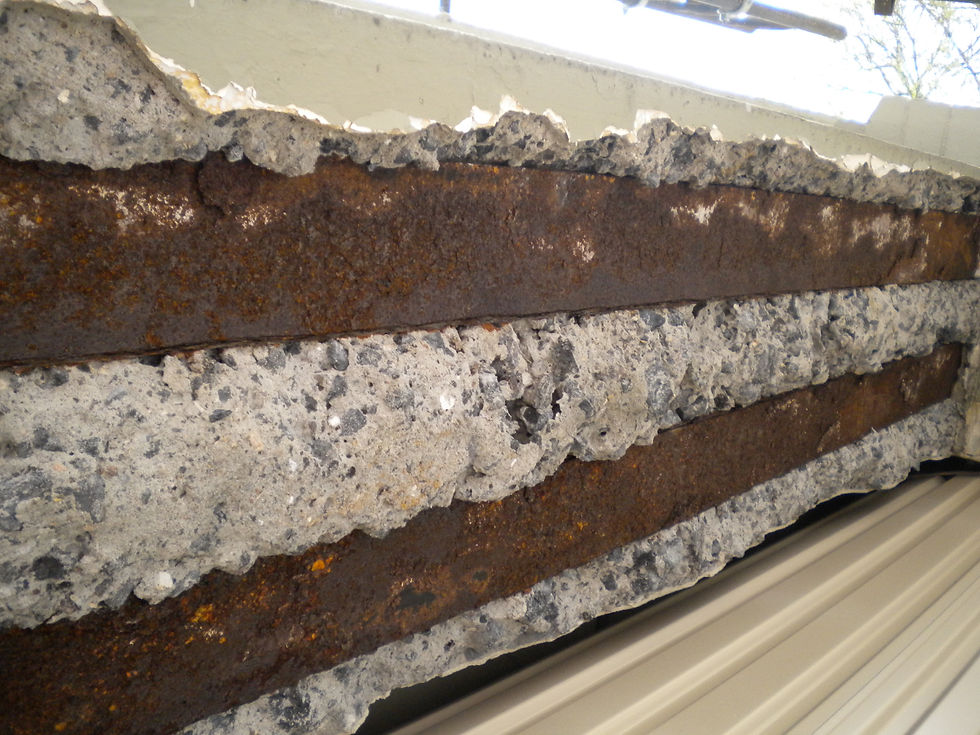
Garage beams to be replaced due to the risk of failure.
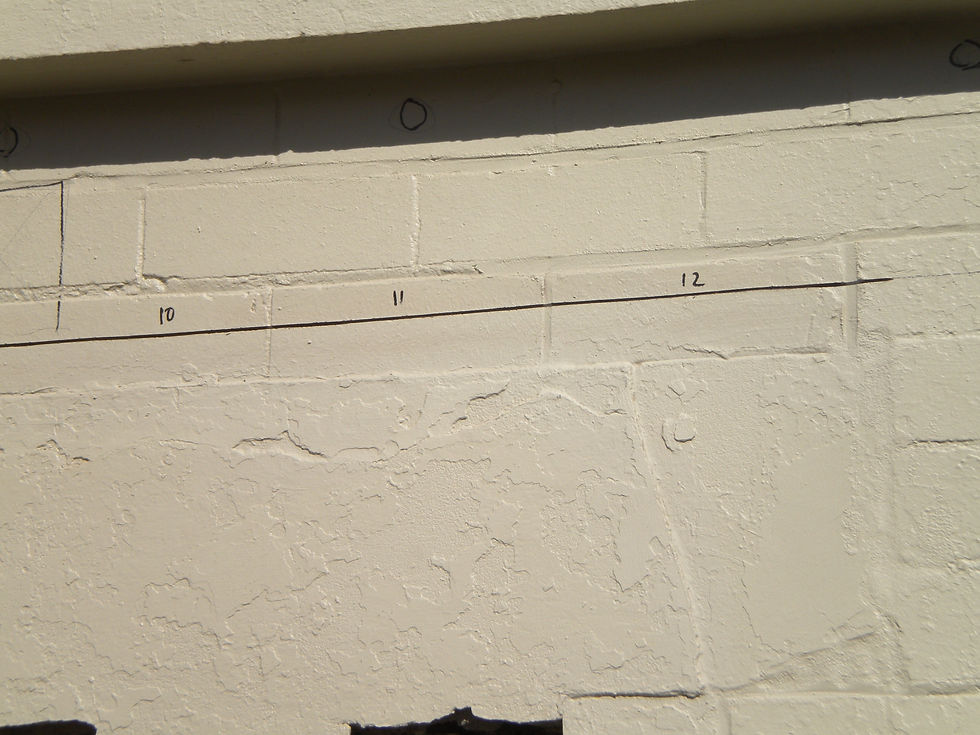
The line of the new beams to counter the building settlement.
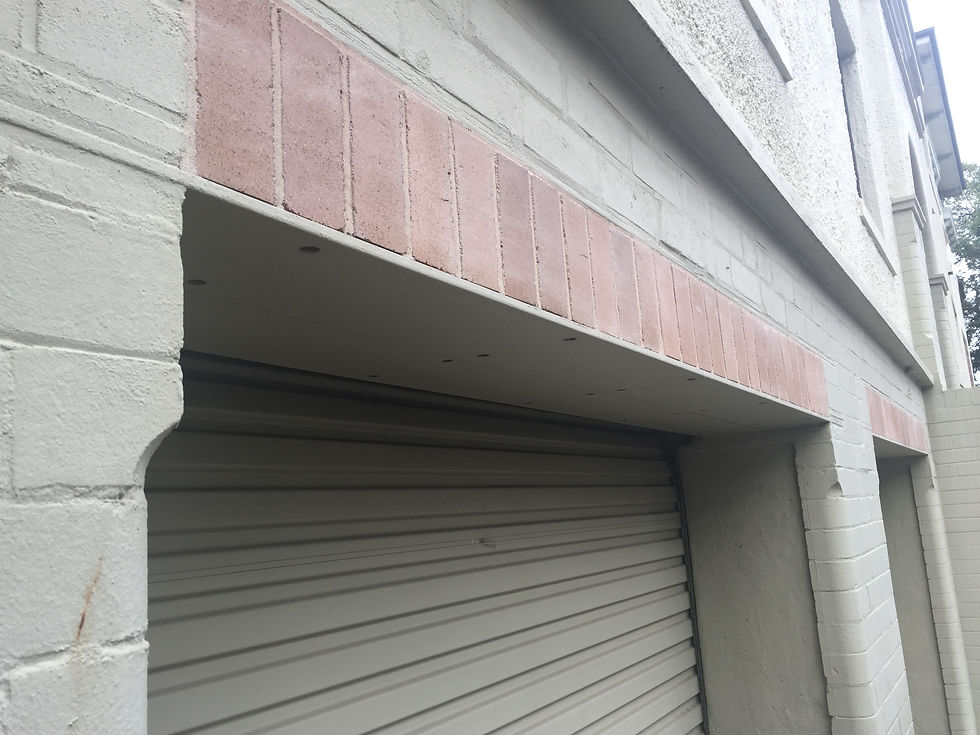
New galvanised steel beams with brick facing.
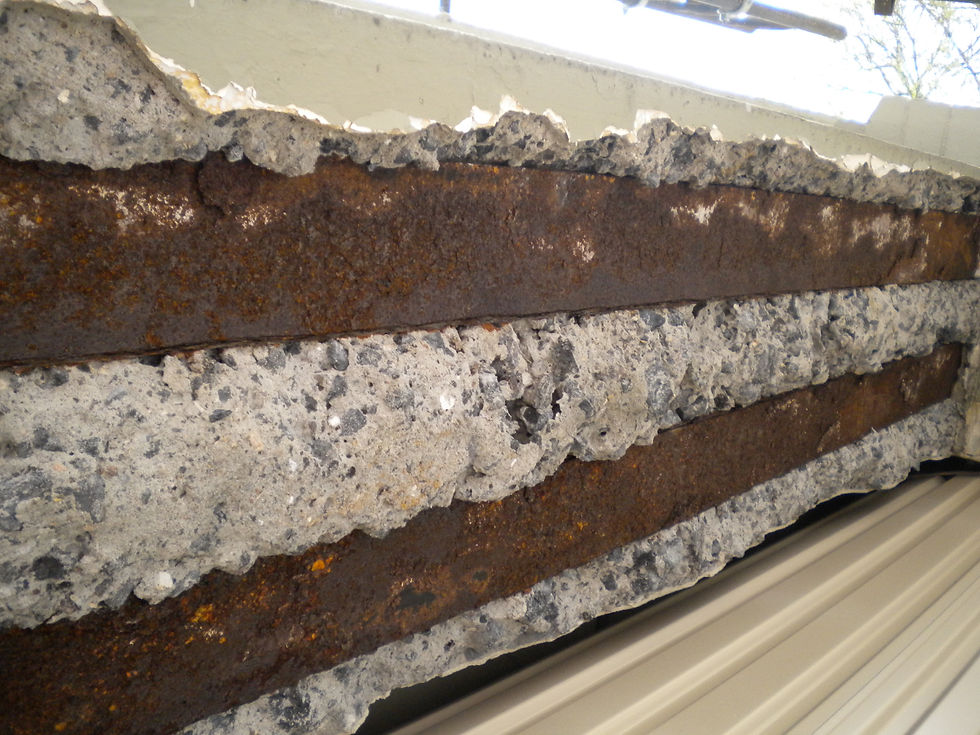
Garage beams to be replaced due to the risk of failure.
Garage beam replacement & electric doors, 2011
The garage door openings were deemed unsafe due to concrete cancer in the original beams.
A total of 8 galvanised steel beams were needed to rebuild the 4 door openings to Lots 2, 3, 5 and 6. This involved opening the asbestos ceilings in each garage to provide access for temporary wall props. The asbestos ceiling to Lot 5 was completely removed, but the asbestos ceilings to Lots 2, 3 and 6 still remain.
Electric garage doors were also installed by J&K Roller Doors.
The work was specified by R Balas Consulting and undertaken by BSR Construction.
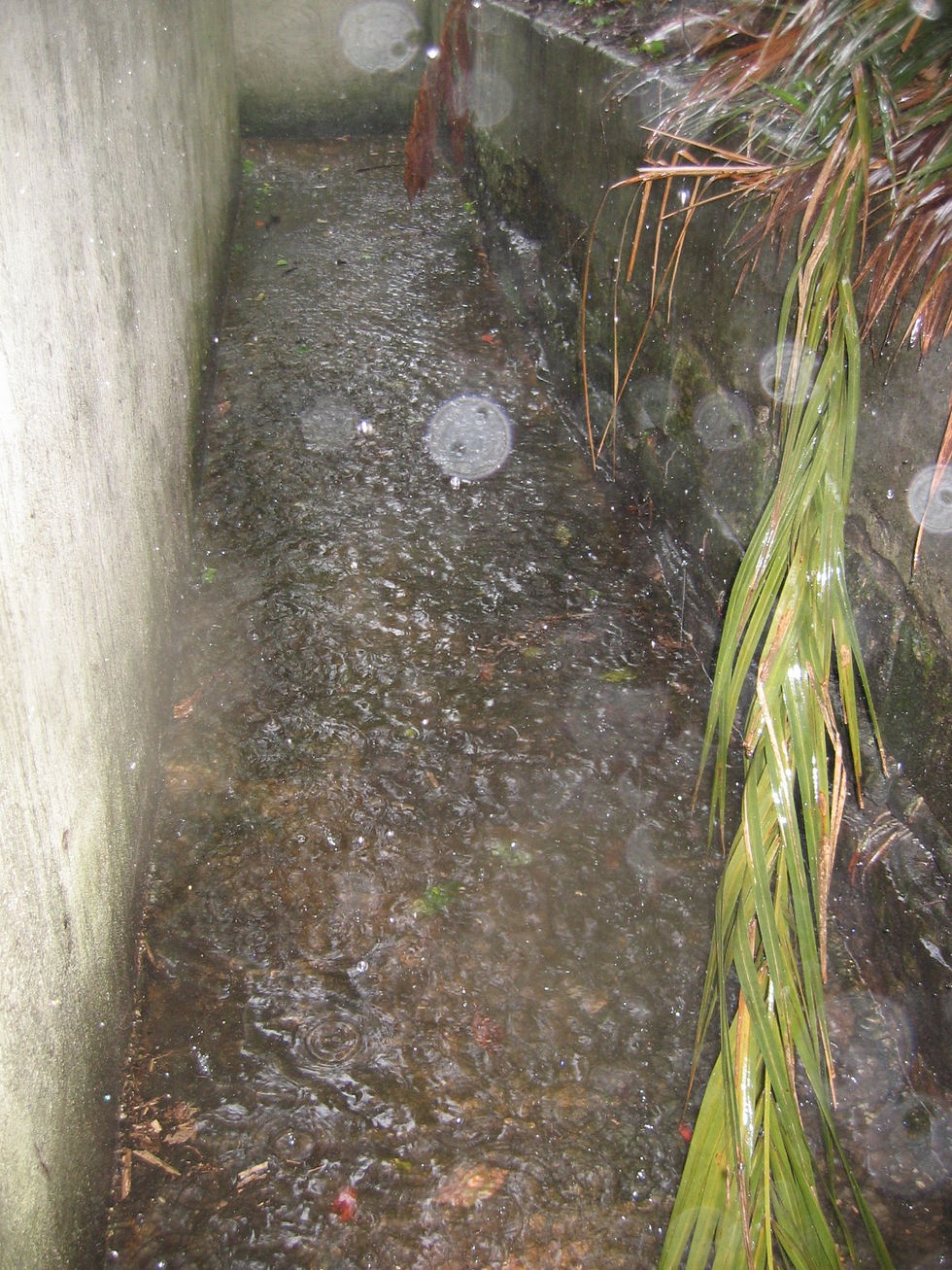
Poor drainage caused flooding of the path.
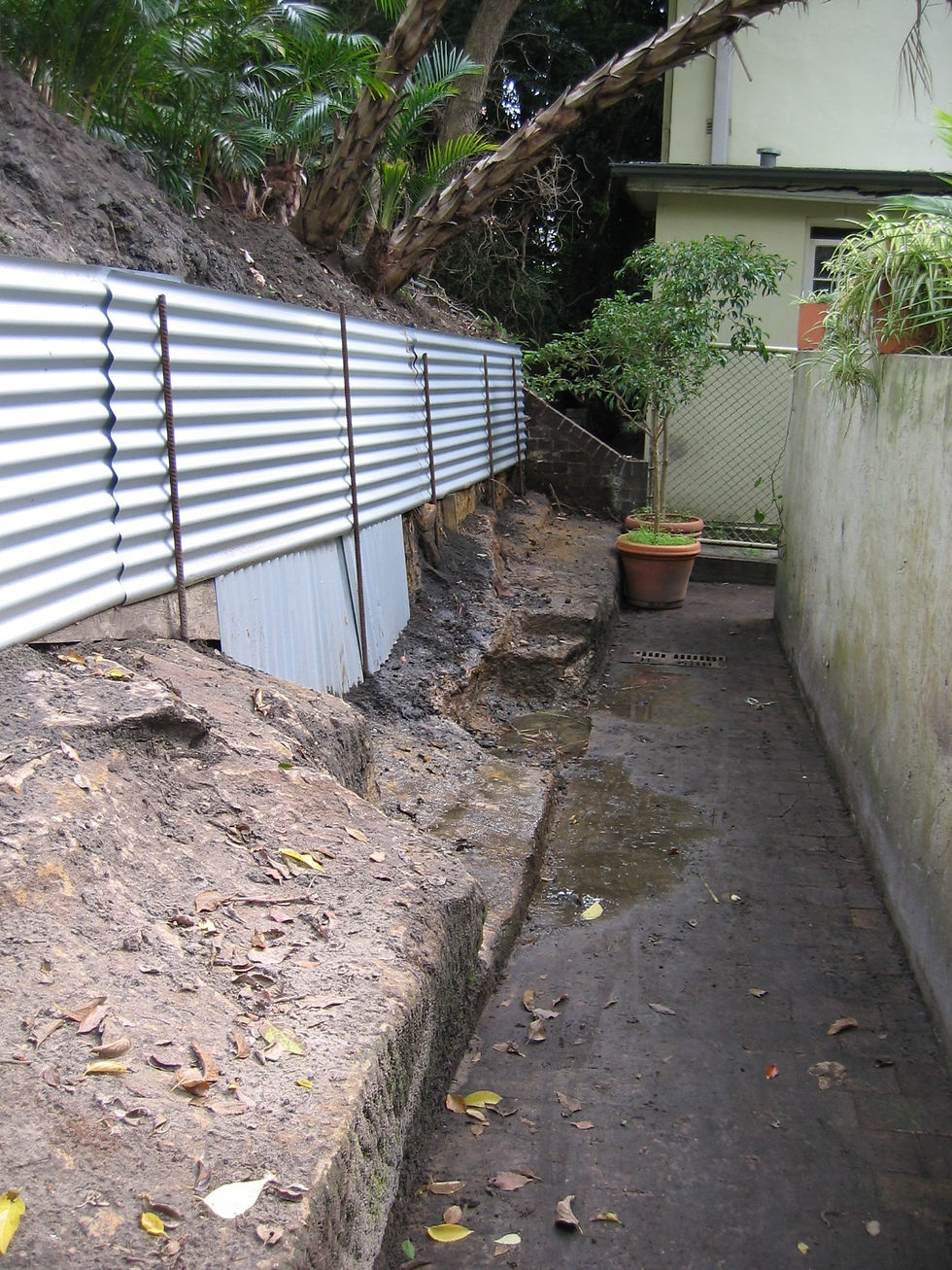
The concrete retaining wall had failed and a temporary wall was built in 2004.

A permanent retaining wall was built and the temporary wall removed.
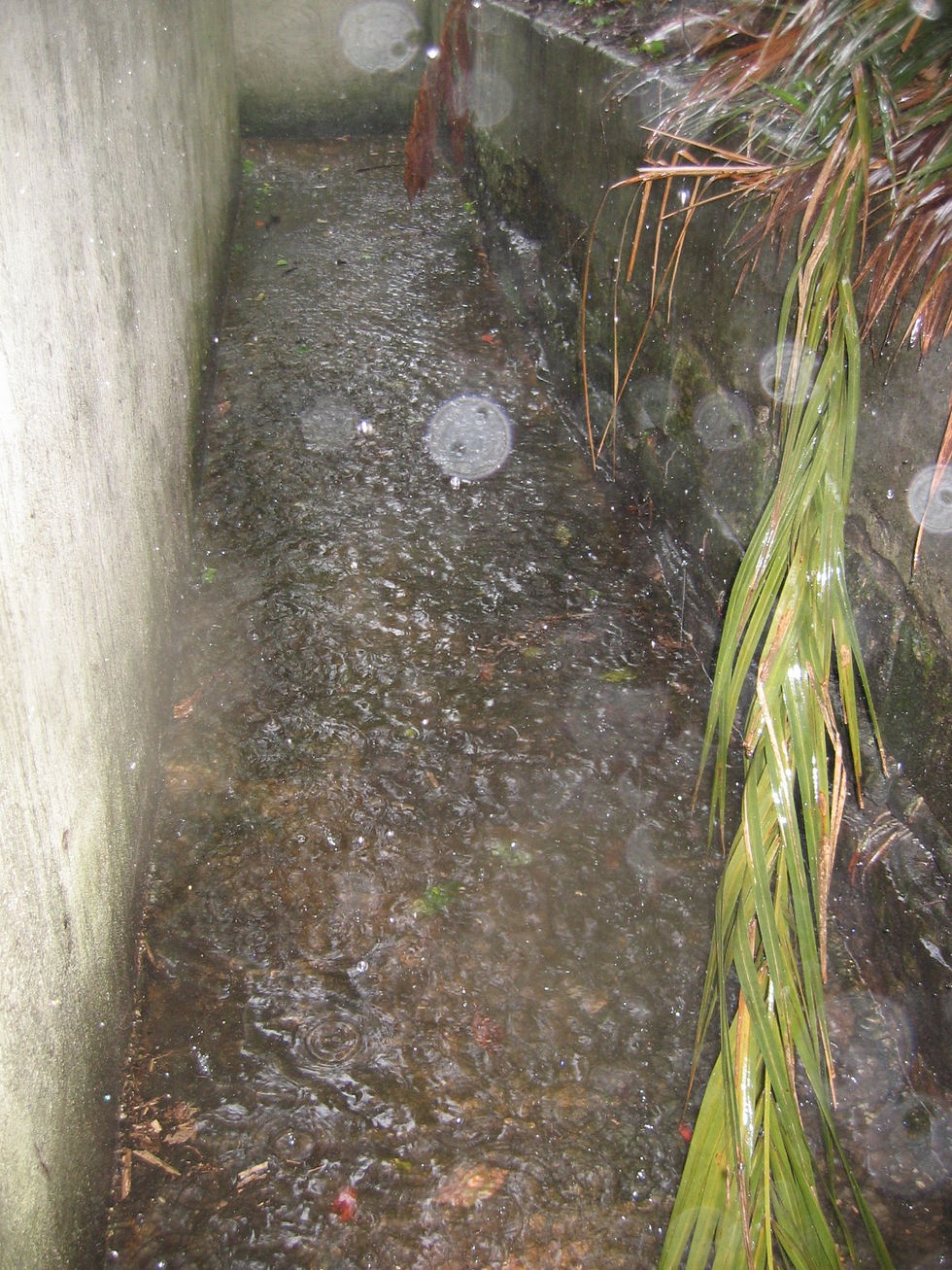
Poor drainage caused flooding of the path.
Western retaining wall & drainage repairs, 2012
The failed retaining wall behind Lot 2 was identified by Chapman Hutchison in 2002, and removed in 2004. The offending tree was not removed until 2017. The area suffered from poor drainage and frequently flooded. Termites were discovered in Lot 2 in 2004 and the level of ground water infiltration was a key factor in attracting the ants to the area.
A galvanised steel and timber retaining wall was built into the rock, and a new drainage sump and soak away installed.
The work was undertaken by BSR Construction and Hunter Metal Work.

Each unit now has its own 6-star rated Rinnai 26 boiler with tempering valve.
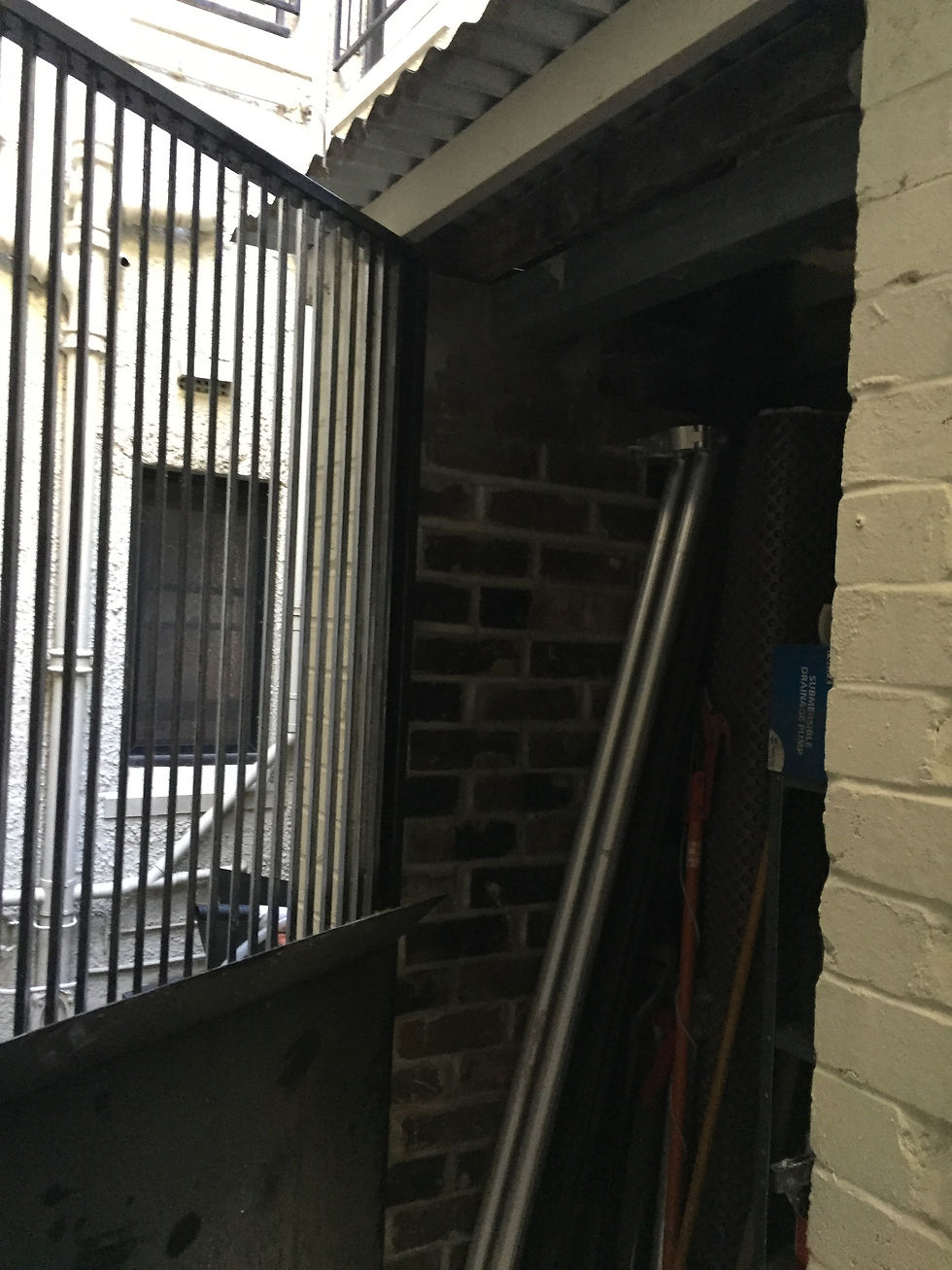
Centralised boiler system was decommissioned and removed.

Each unit now has its own 6-star rated Rinnai 26 boiler with tempering valve.
Hot water system upgrade, 2013
The original hot water system relied on a central boiler and a small bore return network to increase hot water response time. It had the ability to service about 18 persons in the building in peak times, and this was frequently stretched.
To upgrade the ageing system, each unit was provided with its own externally mounted gas boiler, together with a metered gas and water supply. All pipework was hidden inside 2 dedicated shafts inside the wall cavities. Individual unit boilers are Lot property in the Common Property Memorandum.
The work was undertaken by BSR Construction and Rubber Duck Plumbing.
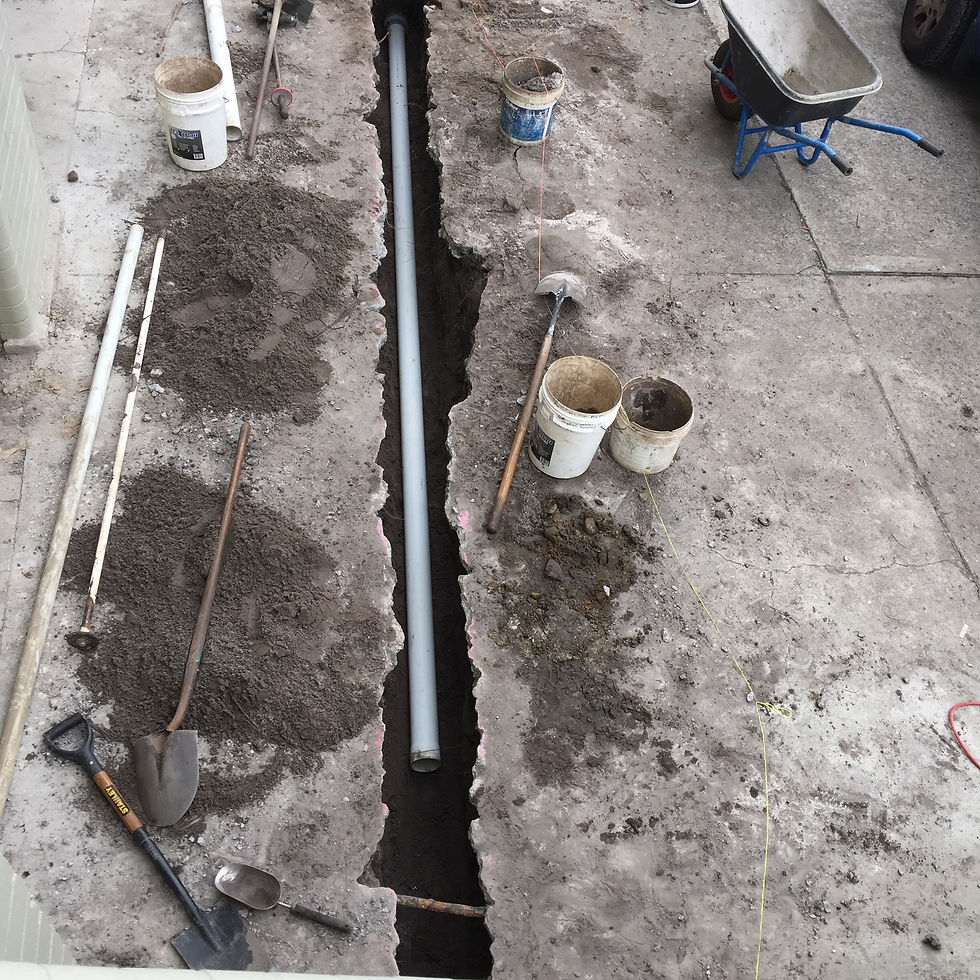
The replacement sewer line starts about 200mm from the boundary trap.

The section under the steps was lined with epoxy and then connected to PVC.
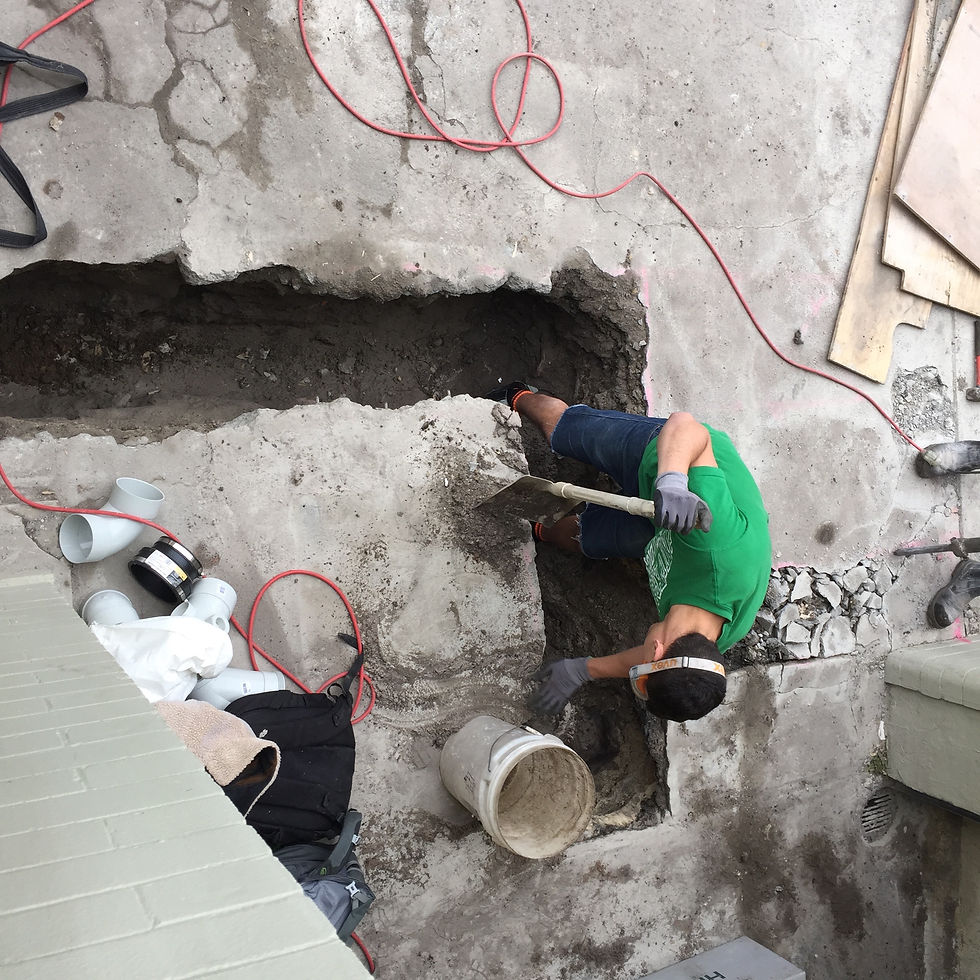
The replacement sewer line was connected to the southern sewer line via garage 5.
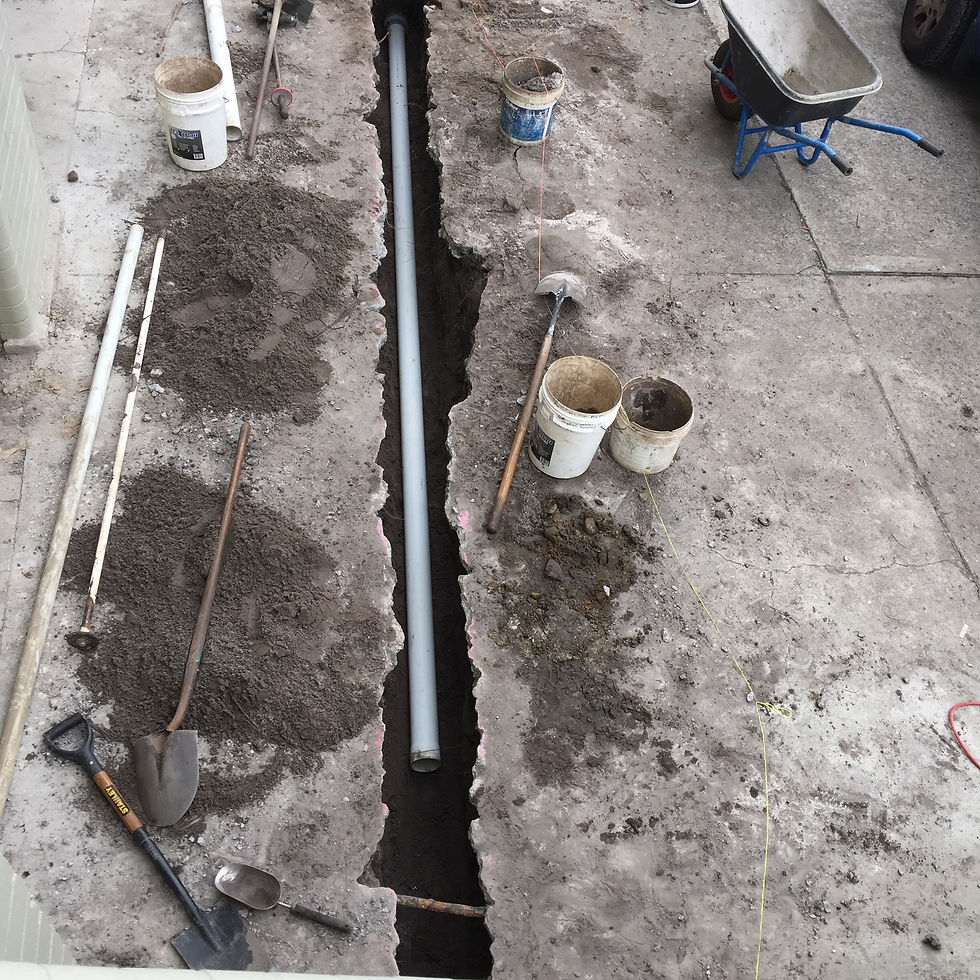
The replacement sewer line starts about 200mm from the boundary trap.
Eastern (front) sewerage upgrade, 2015
The proposed landscaping to the front facade meant that the sewer line needed upgrading to avoid tree root invasion. It had also been identified by Chapman Hutchison in 2002 that the sewer lines needed investigating. Both these goals were achieved, in part, with this project. The 4 metre section of clay pipe under the entrance steps had to remain, but was lined by Pipe Relining Solutions using an epoxy sock and is covered with a 20 year warranty.
The work was undertaken by Rubber Duck Plumbing with funding from Lots 1 & 5. The northern sewer line is still to be upgraded if any toilets are added to those Lots.
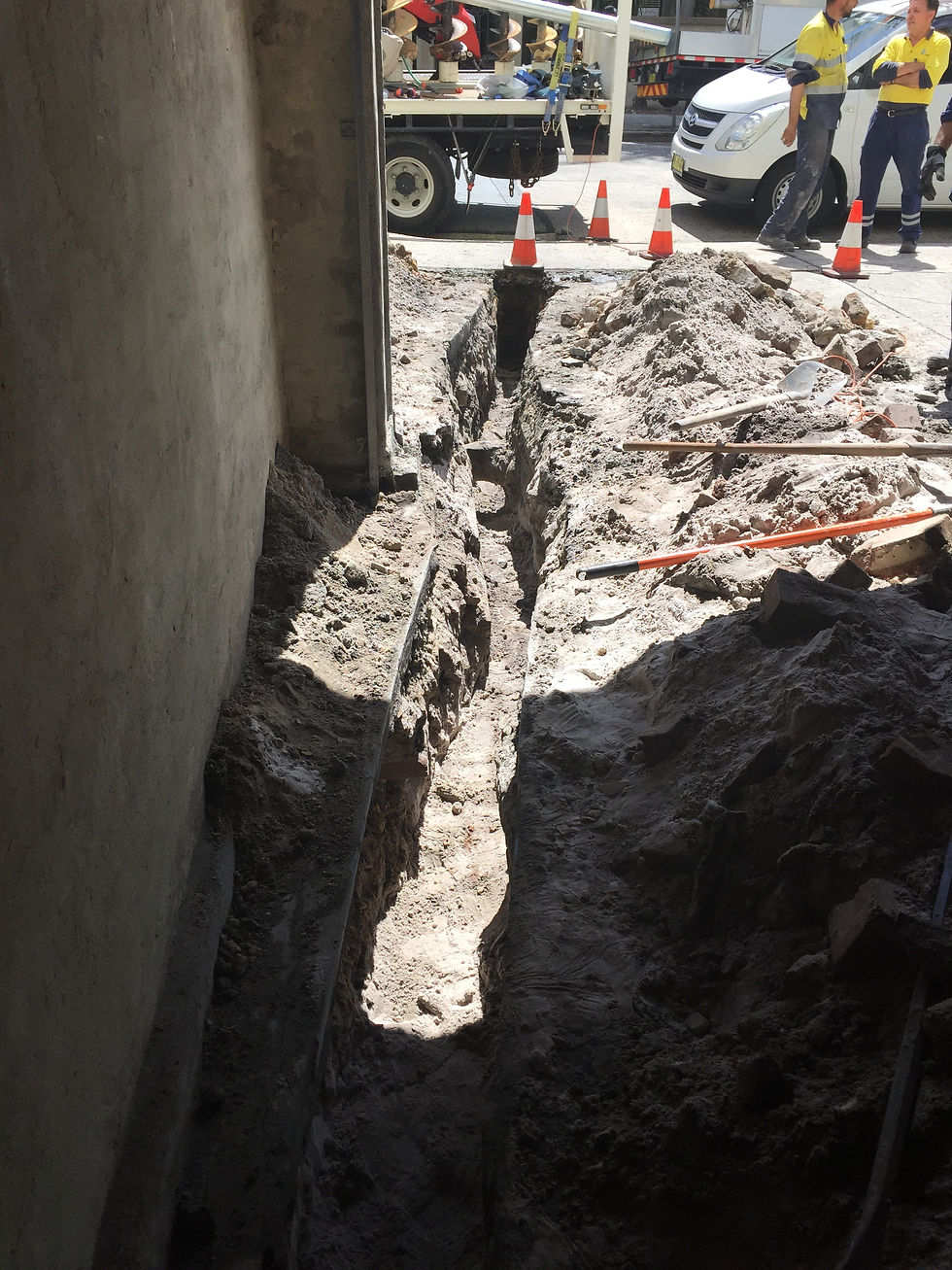
New 25mm cable runs under the courtyard and garage of Lot 5.
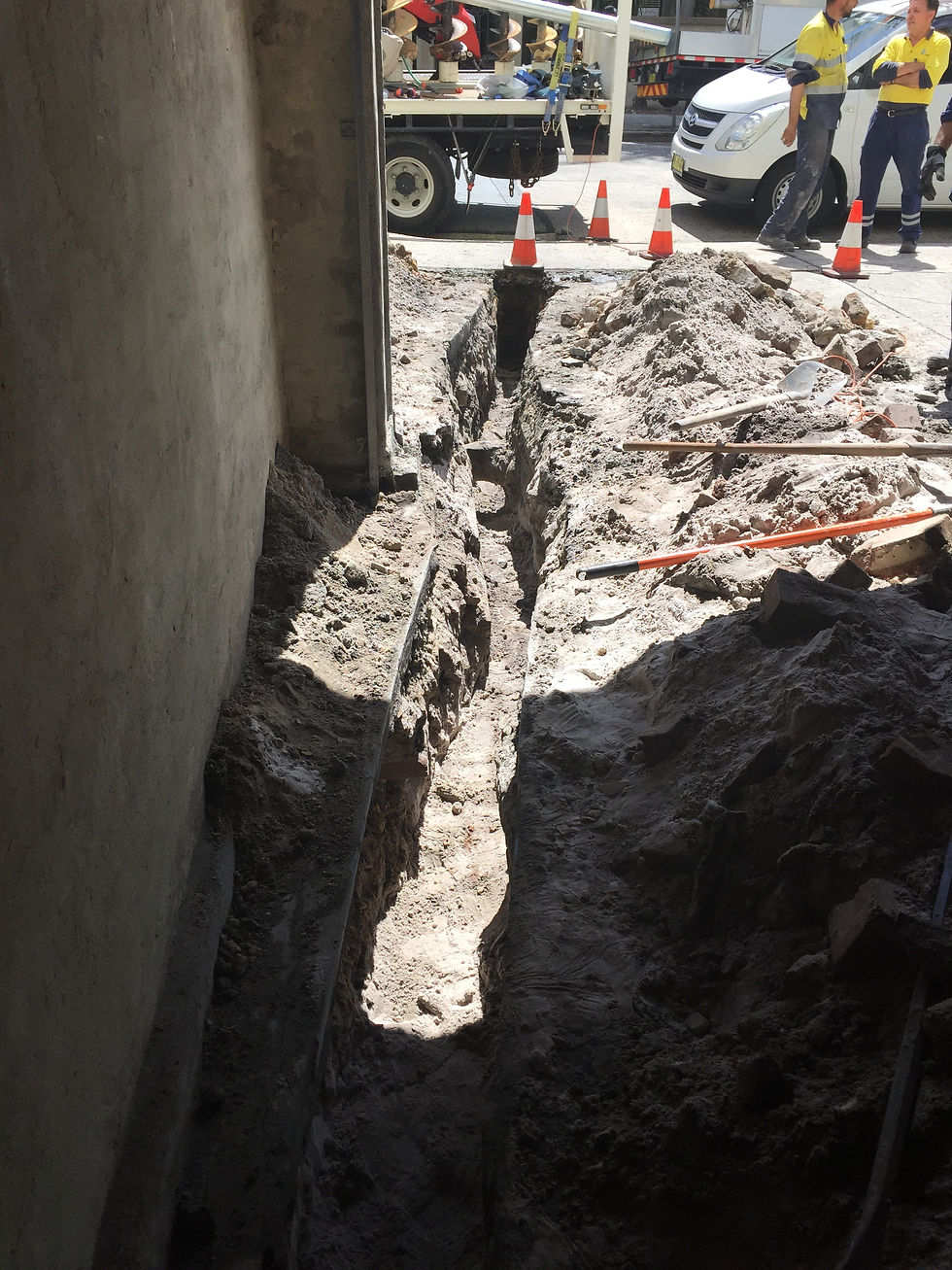
New 25mm cable runs under the courtyard and garage of Lot 5.
Electricity feed upgrade, 2015
A Level 2 electricity service provider upgraded the original 1928 supply cable to the building using a new 25mm 4 core XLPE service cable.
All meter panels were rewired to a new mains switch using 10mm PVC. Each unit is now limited to 50A and safety switches are fitted to all circuits. The only remaining 1928 cabling is in the lighting circuits of units 1, 2, 3 and 4, and the common stair area, but the use of safety switches minimises the risks from old cabling.
The Level 2 work was undertaken by Eris Electrical. The relocation of circuit breakers for each unit into Lot property, and the extension of the 10mm PVC cable into each Lot, has still to occur.
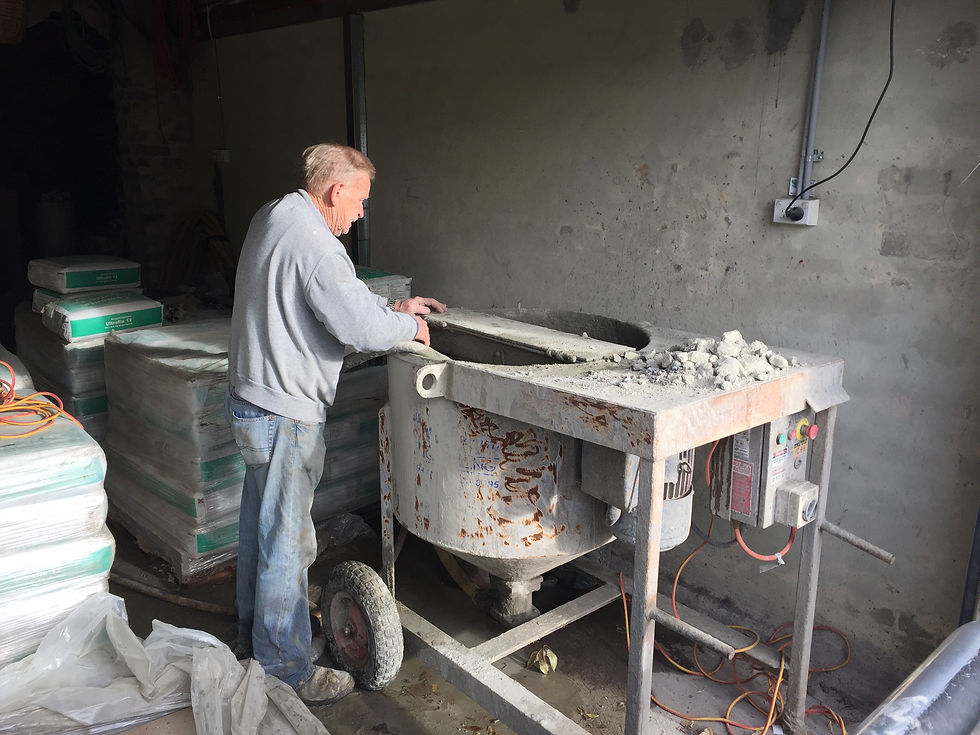
The mixing was done in a garage and pumped to the injectors.

Injection hole on southern elevation, in this case under the timber decking of Lot 1.

Injection holes in Lot 3 courtyard.
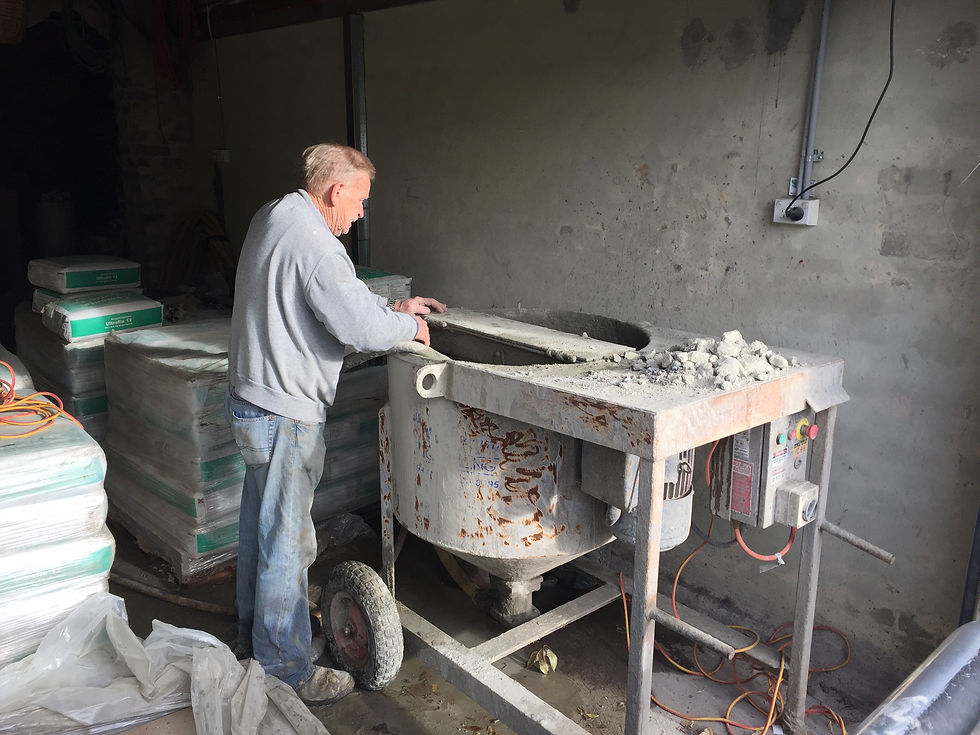
The mixing was done in a garage and pumped to the injectors.
Cement injection to eastern (front) facade, 2015
A cement injection technique was instigated as part of Special By-Law 7 whereby a superfine cement mix was injected into the ground to a depth of 2 to 3m, and this delivers a tensile strength of 5 to 10 MPa.
The work was initiated to safely permit the structural underpinning to the southern side of the building, but was extended to the eastern (front) elevation to stabilise the ground against future movement caused by changing ground water conditions. The load-bearing capability of the ground is not changed and in 2018 new cracking to the eastern (front) elevation started to occur.
The work was inspected by R Balas Consulting and undertaken by GFW Australia, with funding from Lots 1 & 5.
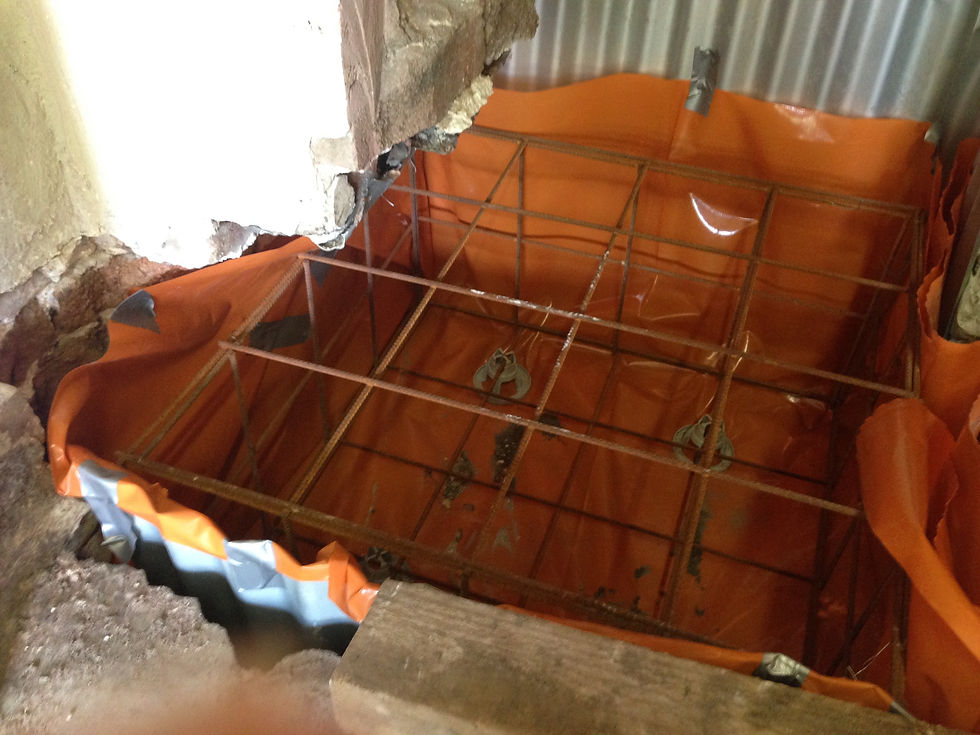
Six columns were underpinned to 2.1m below the original brick footing.

Early termination of underpinning to avoid any new load going onto the rock beneath.

900mm thick concrete pours and brick column underpinning, all to a depth of 2.1m below the original footing level.
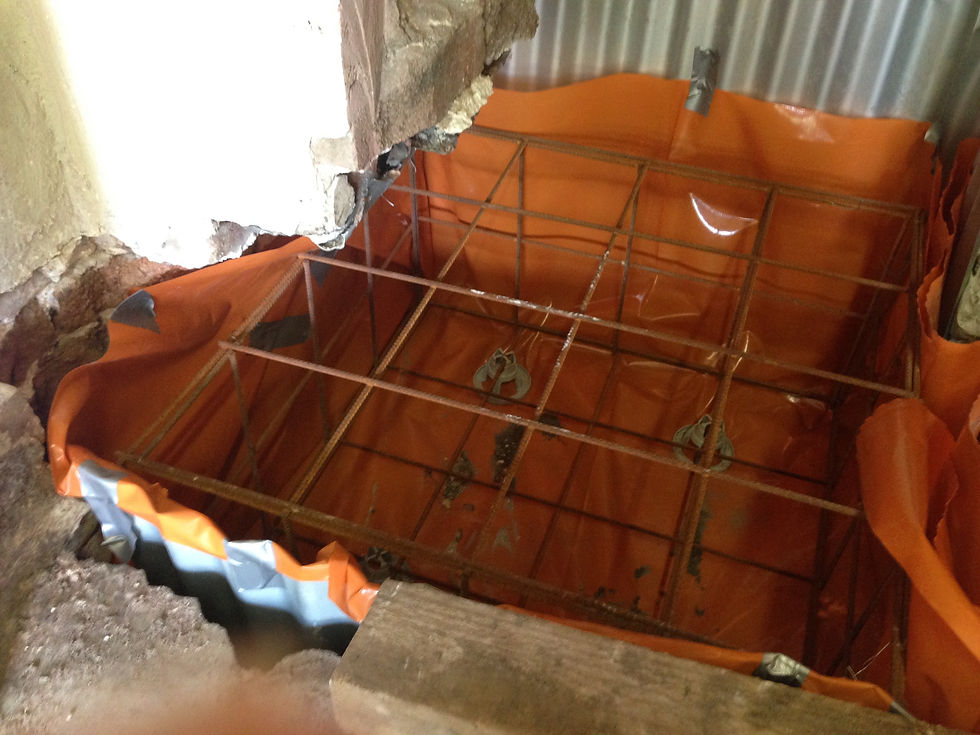
Six columns were underpinned to 2.1m below the original brick footing.
Structural underpinning to southern side, 2015
Although underpinning was not considered cost effective by Chapman Hutchison, it does provide a permanent solution to footing movement if the rock and water conditions permit it. It also becomes a necessity if the load bearing structure is being altered near known footing movement, as in the case of the works described in Special By-Law 2.
To make the underpinning cost-effective, a 40cm deep sub-floor void was offered to all owners as a potential storeroom on the condition that whoever took up the offer underpinned the southern side of the building. Special by-Law 7 covers these works.
The work was specified and inspected by R Balas Consulting and undertaken by ADS Underpinning & Piering, with funding from Lots 1 & 5.
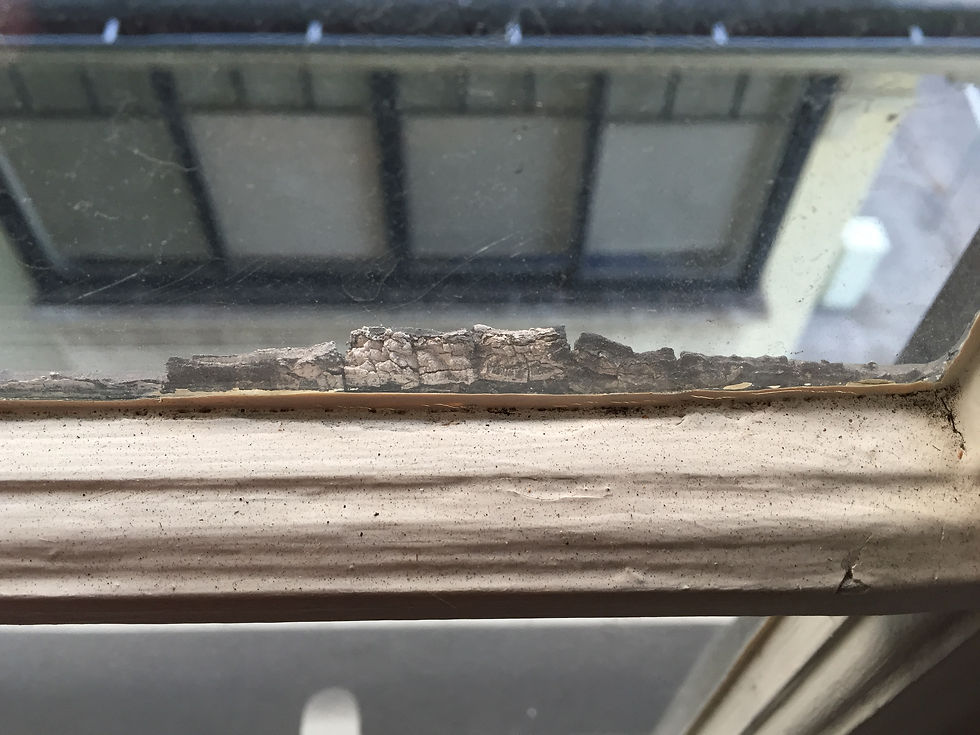
Northern elevation.
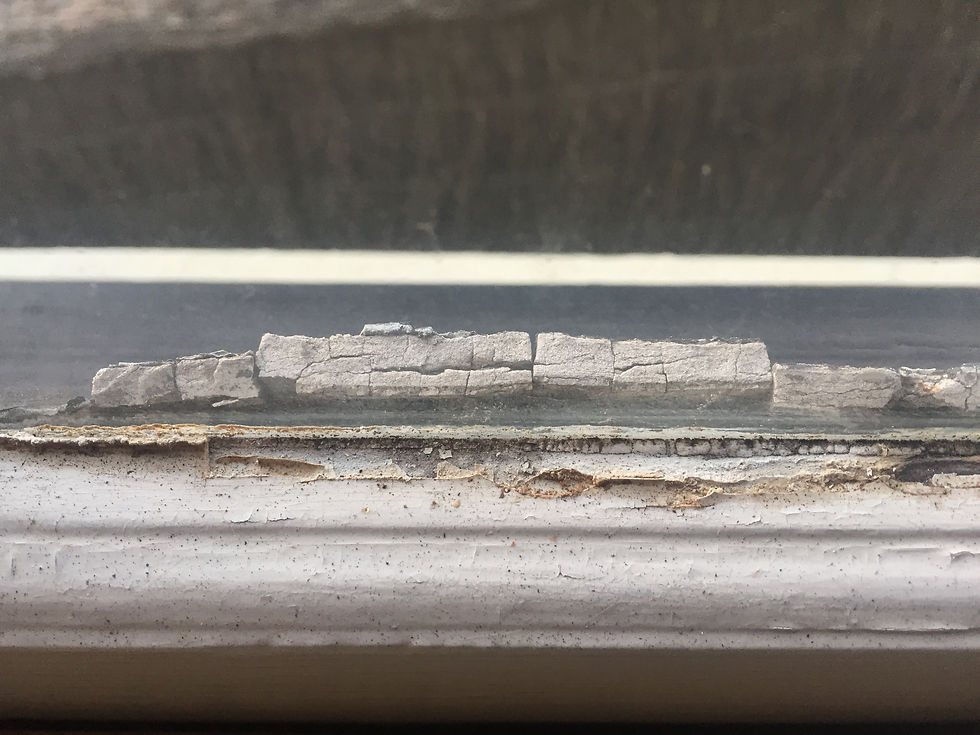
Southern elevation.

A $600 sub-frame replaces the 2 sliding sashes and is sealed within the original timber frame.
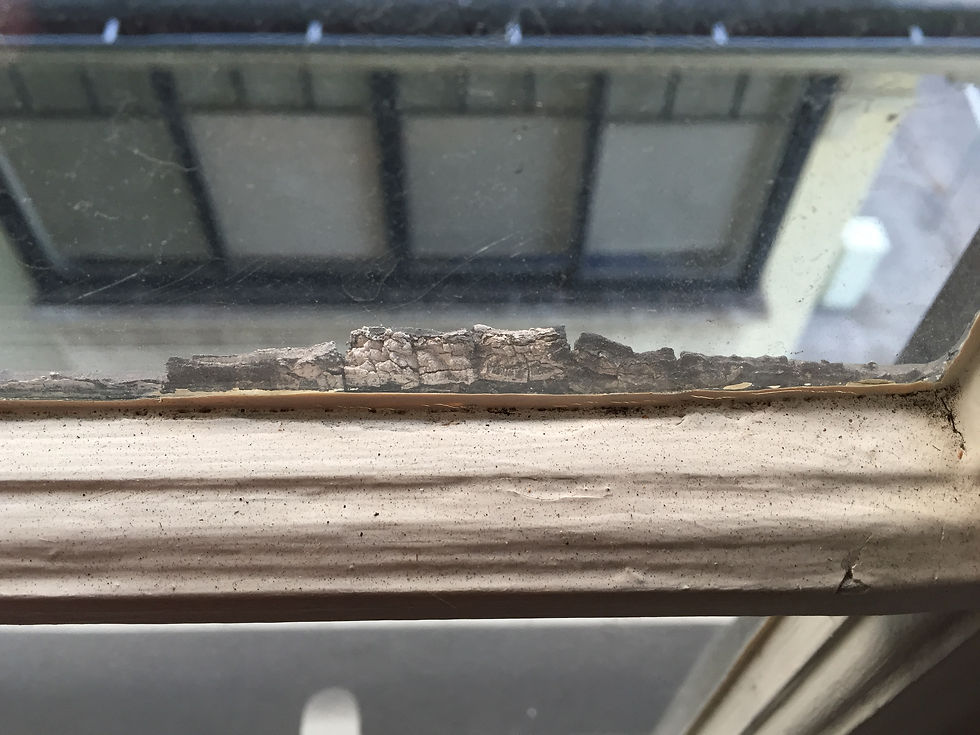
Northern elevation.
Window sash repairs (on hold from 2015)
The windows were raised as a concern by Chapman Hutchison in 2002 and repainted between 2007 and 2010 with new timber quadrants. Whilst the sills and frames remain in good condition, except for a couple adjacent the old window boxes, the sashes need further repairs.
Five windows have so far been upgraded by owners using Special By-Laws, and in 2015 an aluminium sash sub-frame was trialed in a single window which allowed the original timber frame to be kept. But this upgrade solution was rejected by owners.
In 2018 an independent opinion on the windows was obtained. The main risks are water impregnation and the lack of 3mm glass (6mm in bathrooms).
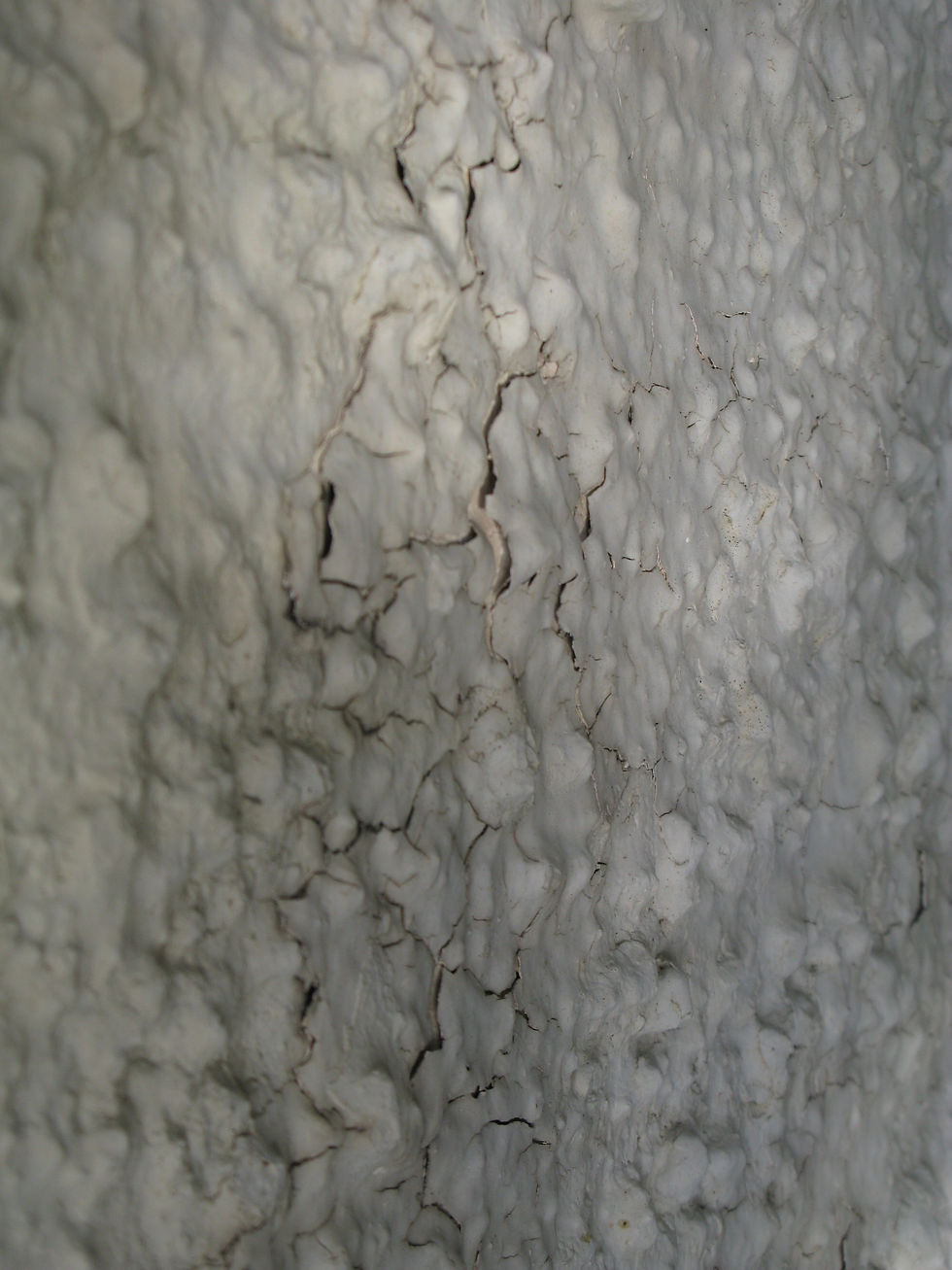
Membrane damage in 2015

Membrane damage in 2018

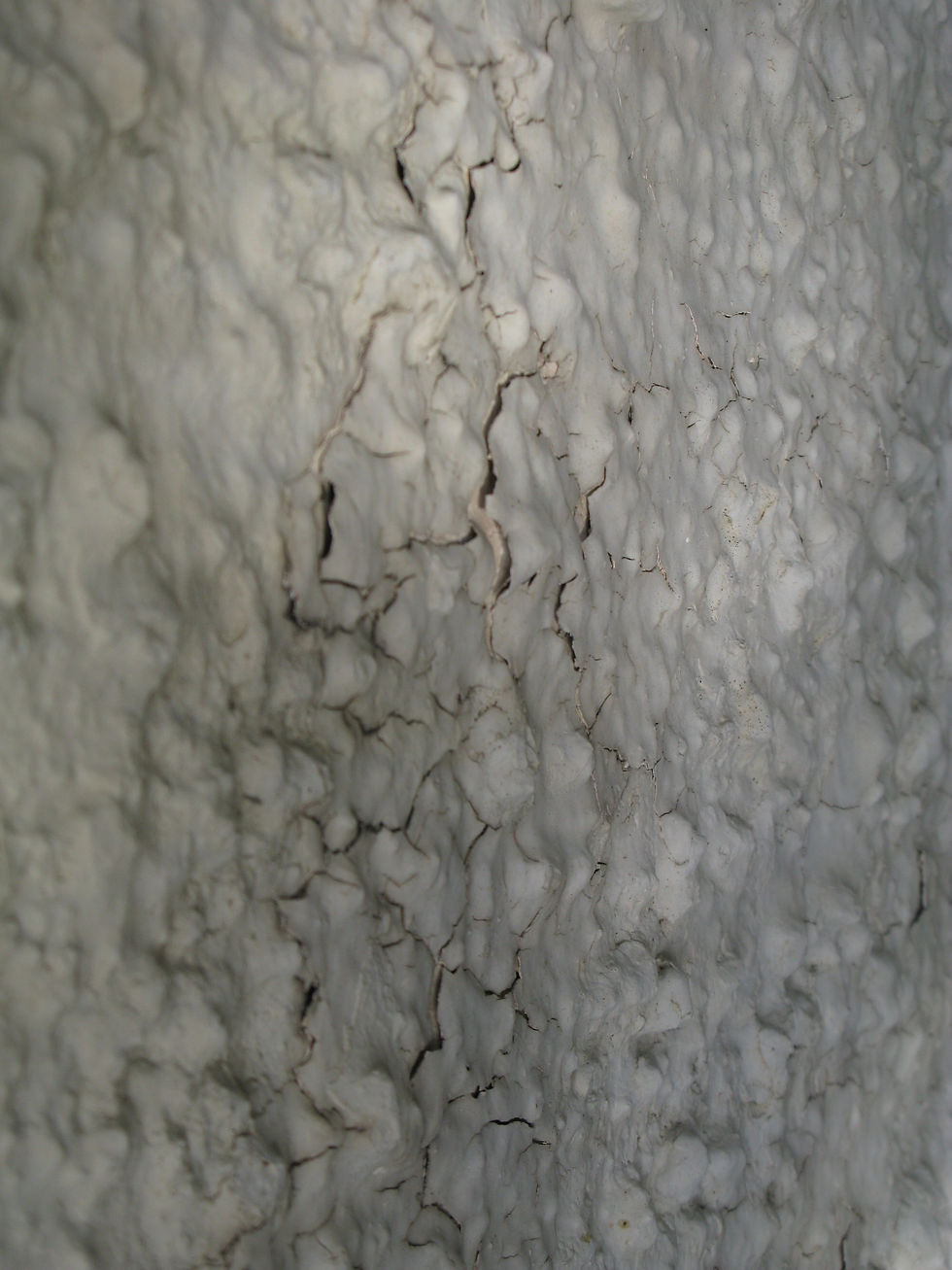
Membrane damage in 2015
Membrane repairs (on hold from 2015)
To abate the influx of rainwater into the structure, the building membrane was renewed between 2005 and 2010 as part of the staged works to each facade. The Dulux specification relied on water blasting to remove the old calcimine base paint, X10 Weathershield as a primer, and AcraTex AcraShield as a top coat. The window sills were painted in oil based enamel but then sealed with X10 Weathershield in 2012.
A lime mortar brick building with shallow brick foundations is vulnerable to high levels of movement and membranes need checking every 10 years. In 2015 the membrane started to show signs of damage and in 2018 new cracks were noted by engineers which will allow the ingress of water, lime mortar erosion and ultimately brickwork failure in the load bearing walls.
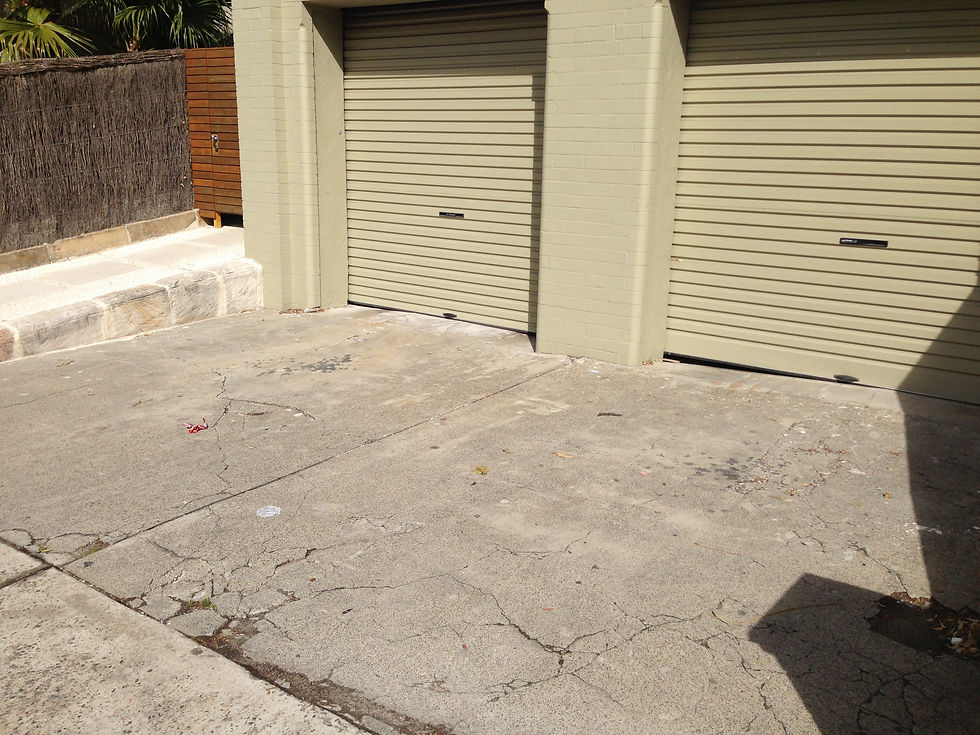
Suffered from extensive cracking and poor drainage.

Removing old material to the new level.

Magnolia trees, Japanese buxus hedges and cast iron urns.
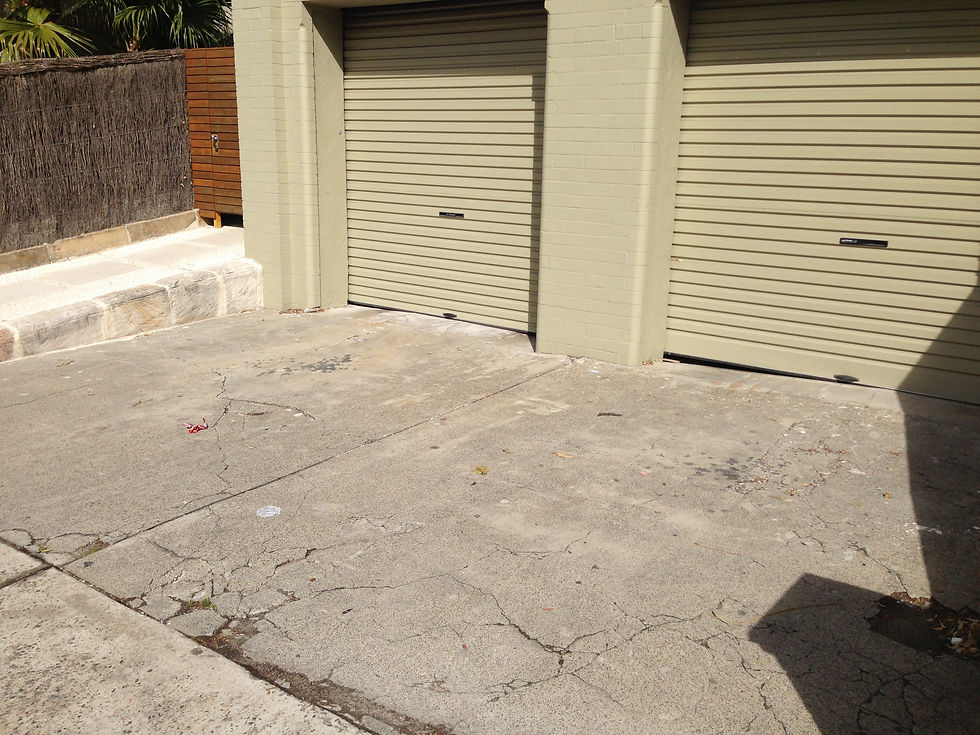
Suffered from extensive cracking and poor drainage.
Driveway repairs & landscaping, 2016
The driveways were raised as a concern by Chapman Hutchison in 2002, and so after upgrading the eastern (front) sewer line and electricity feed the driveways to Lots 2, 3, 5 and 6 were excavated and road base added and compacted to new levels. The new concrete slabs were poured to a depth of 200mm using SL82 mesh and 32 MPa charcoal concrete.
Openings in the concrete were provided for planting 8 x Magnolia grandiflora "Kay Paris" and 160 x Buxus microphylla "Japonica". Provision was also made for Hunza lighting and Galcon irrigation.
The work was designed by Bay Street Gardens and R Balas Consulting, and undertaken by City Concrete, TM Services and Plantbiz.


Second bathrooms (blocked in 2018)
Second bathrooms (DA53/2016) rely on new drainage for sewerage and stormwater, as well as gas, electricity and cold water supplies passing through the courtyard of Lot 2 (property which can extend 3m below ground).
The depth of this new drainage is a function of the foundation design for Lot 2's extension (DA32/2017), which together with their own drainage design needs to be approved by Council before anything can be built.
All owners are reliant on Lot 2 to install the drainage needed for the second bathrooms without compromising their own development. Council's approved drainage design for the south-side of the building has been updated to show the new north-side drainage.
However, in 2018 the compulsory manager passed a Special By-Law for Lot 2 that excluded any drainage, and this effectively blocked the plan for second bathrooms.
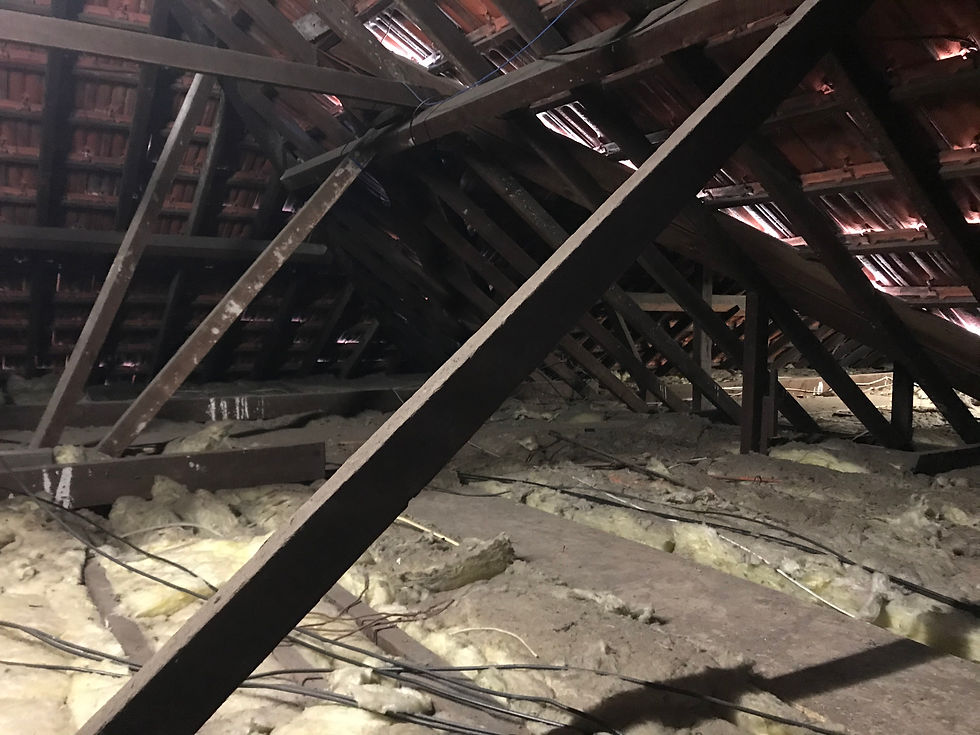
The roof timbers are slowly moving due to the iron nails rusting over 90 years.
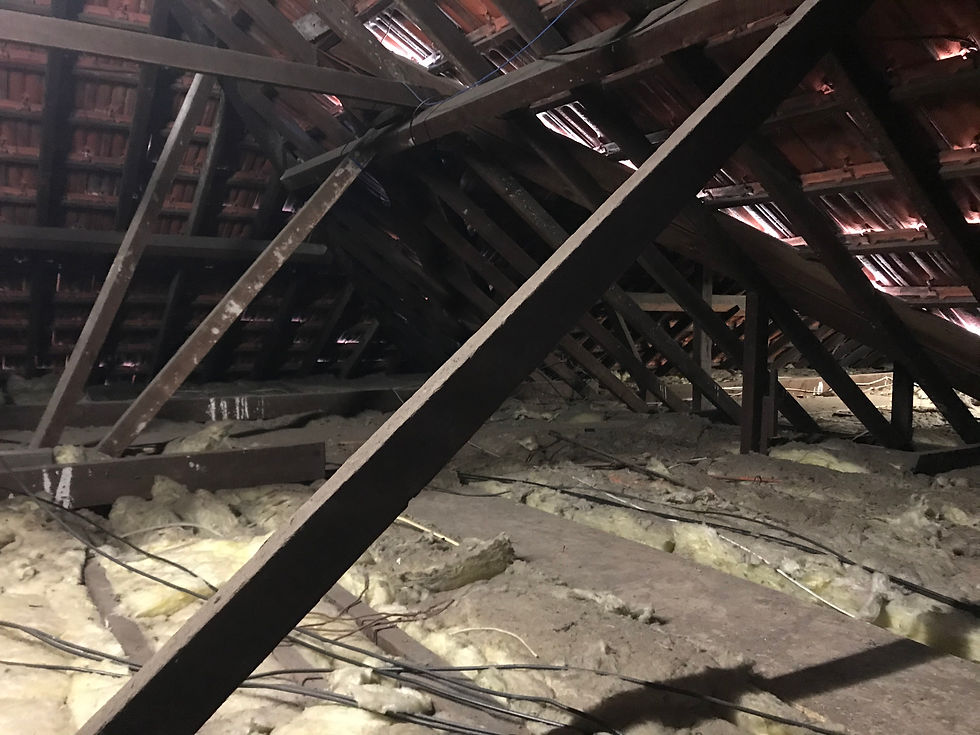
The roof timbers are slowly moving due to the iron nails rusting over 90 years.
Roof truss sagging (on hold from 2018)
In the Chapman Hutchison Update in 2018 it was identified that the timber to timber connections to the roof framing were moving as a result of the 1928 wrought iron nails rusting in the humid roof environment. This is likely to lead to eventual and sudden failure if not corrected.
The structural engineer specified "triple-grip" connectors and new galvanised nails. After further inspection, the proposed solution by the roofing truss carpenters is to also add, in addition to the "triple-grip" connectors, some galvanised bolts to the main tensile stress areas and some additional recycled structural oregon uprights.